Military UAVs tackle performance issues under SWaP-driven designs
StoryApril 15, 2019
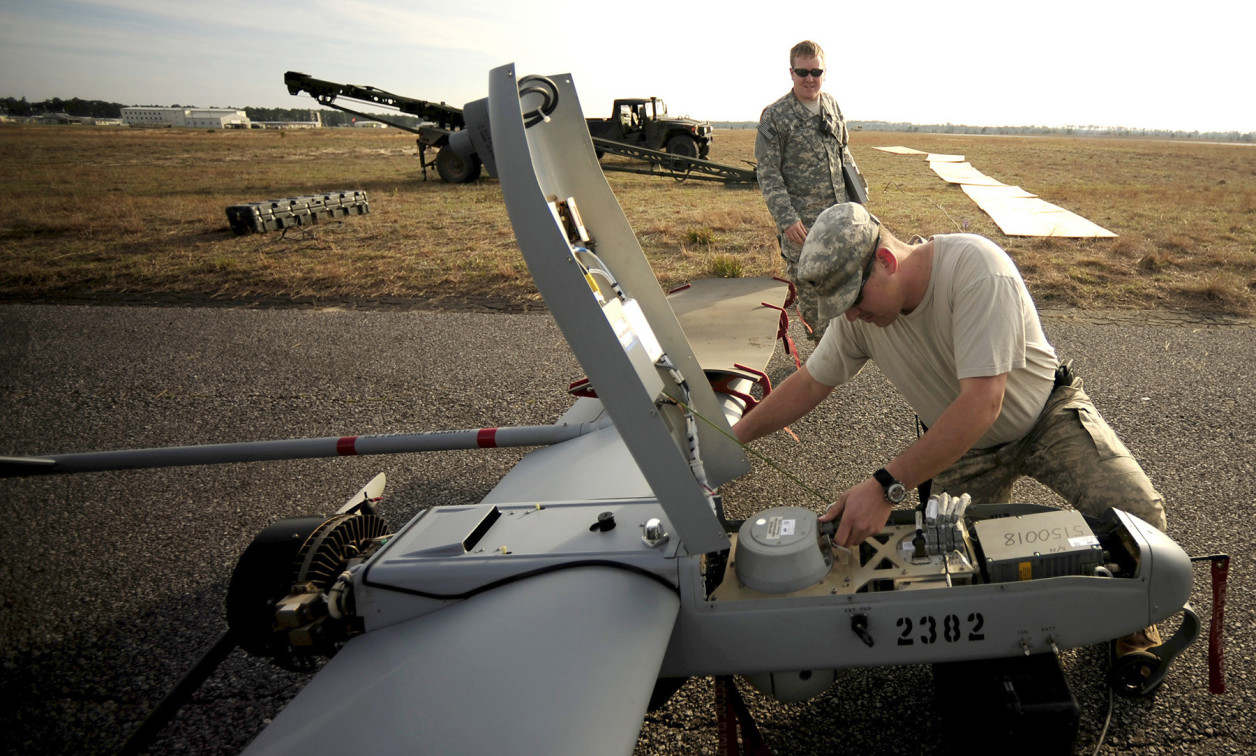
The U.S. Department of Defense (DoD) is seeking high-performing unmanned aerial vehicles (UAVs) designed to meet stringent size, weight, and power (SWaP) constraints. One solution is to pack the vehicles with components. The problem? The lower the SWaP and the smaller the UAV gets, the more performance suffers.
Unmanned aerial vehicle (UAV) designs are increasing the number of onboard RF [radio frequency] and microwave components to address performance issues and tackle technical challenges ranging from counter-UAV tech to power consumption. To address these challenges, UAV developers are integrating different technologies to deliver a high-performing UAV in a design constrained by size, weight, and power (SWaP) concerns.
UAVs in particular are “incredibly challenging because the radar cross-section is fairly low. The only thing they really reflect are the little engines on the rotors,” says Doug Carlson, senior vice president and general manager, RF & Microwave business unit, MACOM (Lowell, Massachusetts). “Detecting UAVs effectively at a distance in order to give the user time to react is turning into a very hot topic in the field of radar and RF.”
The rise of UAV and counter-UAV technology is pushing UAV developers to ask some much-needed questions, Carlson says: “How much RF and how much sensing is going into this counter-UAV problem? UAVs are now a weapon system, both in defense and civil airspace, or civil domains, such that we have to come up with cost-effective and very reliable solutions to counter malicious attacks. We are suddenly seeing the flip side – we’ve done a great job making UAVs and now UAVs are a problem.”
Unmanned systems developers still have quite a few technical challenges to still address aside from counter-UAV problems. For one, “unmanned systems are becoming more and more autonomous,” Carlson adds. “As they become more and more autonomous that means that the sensor capabilities are going to have to go up. The sensor capabilities are going to have to be able to work in all environmental conditions. That tends to lend itself towards RF solutions. I think you’ll see even more RF ending up on unmanned vehicles.”
As unmanned systems become more and more autonomous, and with RF components increasing and at the same time the overall size of the UAV shrinks, users “want more performance (sensitivity, dynamic range, bandwidth, channel count, processing power) for less SWaP. Whatever the current state of the art can deliver is never quite enough to satisfy,” says Jeff Hassannia, senior vice president of Business Development, Strategy, and Technology for Cobham Advanced Electronic Solutions (Crystal City, Virginia). “This is a very big challenge, especially as missions are expected to get bigger and require more performance and new features such as jamming resistance, radiation interferers, the ability to execute multiple missions with single payloads, and more.”
Designing a UAV under the SWaP umbrella is a major – if not the biggest – challenge for design engineers to ensure that this system is stable and powerful enough to complete a mission. “One the biggest technical challenges that we see our customers already trying to tackle is that as you get smaller and smaller you have so much gain; the real challenge is keeping the whole architecture stable,” says Gavin Smith, product marketing manager at NXP Semiconductors (Phoenix, Arizona).
Moreover, UAVs come in various sizes. With “the larger UAVs, the challenge is not whether there is enough power available, but rather heat dissipation,” Smith says. “Sometimes they want to make a very small package for a full module. The higher efficiency, the less heat that’s dissipated and the smaller the product can be. As you probably can appreciate, size is very important because of how much is being crammed into a very small vehicle including communication components, and in some cases there’s data recording, a video component, and UAV controls. All of that stuff requires higher efficiency.”
The drive for higher efficiencies is not new but it is a key factor to delivering a complete solution to the end user. Smith adds, “We also consider battery consumption. Some of the smaller UAVs, pretty much the handheld UAVs, run off battery, so the efficiency is very, very important, as well as the weight.”
In addition to delivering an efficient system, getting some actionable intelligence back from it is a challenge because “High-definition video is becoming more prominent,” Smith explains. “That means higher data bandwidths, which requires more signal bandwidth, which also makes it more challenging for us [to build].”
“In general, in the entire field we’re also seeing a trend towards a higher degree of digitization,” Carlson adds. “What do I mean by that? The information that users get from the air platform, we’re not going to receive it or broadcast it, but I’m very quickly going to digitize that signal onboard and turn that signal from raw data to information. That way, I’m broadcasting information back to the command center rather than just raw data. The design is driven by the fact that there is so much data flowing into these vehicles, so we’ve been able to condense it down and take advantage of the bandwidth pipe.”
Companies are positioning themselves to handle current and future technical challenges. For example, Cobham’s “Waveguides will remain an important element of RF communications and ISR [intelligence, surveillance, and reconnaissance] applications for the future, as waveguide efficiency still makes it the best choice for many applications. In future UAV systems, reduction of system size and weight will be crucially important,” Hassannia says.
Traditional manufacturing techniques have constrained the design of waveguide assemblies of filters, diplexers, duplexers, and antennas resulting in extended assemblies of numerous waveguide elements, he continues. “Cobham is working with additive manufacturing technology that will be a game changer for the packaging of complex waveguide architectures. By removing fabrication constraints and allowing the creation of complex architectures that ‘fold back on itself,’ system volume can be reduced, and the waveguide assembly more easily customized to the host vehicle.” (Figure 1).
Figure 1:Cobham waveguides. Photo courtesy of Cobham.]
(Click graphic to zoom)
|
Integrating tech to achieve max results.
Integrating different types of technologies to deliver a high-performance system will be key for the warfighter. Of course, it doesn’t negate the fact that as unmanned systems become more integrated with all the additional RF components to meet high data demands, there is still the DoD’s SWaP directive.
Without a doubt, UAV design trends toward integration, Hassannia says. “What was once a box is now a board, and someday it will be a chip. Today’s highly integrated solutions are made possible by high-performance direct digital back-end solutions based on system-on-chip FPGAs [field-programmable gate arrays].”
“With size, if we move to the integration phase, for example, it would be about using an IC [integrated circuit] as opposed to a multichip module,” Smith says. “The size of the device along with the size of the matching network on the PCB, the printed circuit board that’s required, if we do a lot of internal matching in the IC, then very little is left to be done outside, which allows our customers to shrink the overall size of the package they’re housing.”
Unfortunately, adhering to SWaP requirements hurts system performance. To achieve peak performance within SWaP constraints, MACOM is focusing on higher levels of integration, Carlson says. “We tend to focus on heterogenous forms of integrations, in other words bringing multiple technologies together to form a highly capable, compelling solution. Often, if I integrate in a silicon platform or something like that, I compromise certain RF functionality. Sure, I get the integration, but I degrade performance. And most of the things we’re addressing, the performance is as critical a requirement as weight and cost.”
“SWaP optimization is definitely a major design challenge in this space,” asserts Deepak Alagh, senior director and general manager, Mercury Systems RF & Microwave group (Andover, Massachusetts.) “As we shrink high-frequency circuitry into very small spaces, accurate modeling becomes very critical and difficult. In addition to modeling and accounting for cross-coupling, the models need to capture nonlinear effects as well as the heat generated in the devices.
“Recently, we have been seeing an increase in requests for both high power density and high integration density,” Alagh adds. Users are leveraging “GaN [gallium nitride]-based amplifiers to maximize the RF output power while minimizing the module size. Additionally, instead of developing multiple separate modules, our customers are asking us to integrate multiple capabilities in a single, compact housing.”
For example, Mercury Systems’ Mercury’s “SpectrumSeries Platform combines RF, digital, and custom SiP in a small outline,” Alagh says (Figure 2).
![]() |
Figure 2: Mercury Systems’ SpectrumSeries Platform. Photo courtesy of Mercury Systems.
(Click graphic to zoom)
Thankfully, “the advancements in semiconductor performance and chip-scale integration have had a very dramatic impact on the receive side of the system, resulting in maybe a 10:1 reduction in size and power consumption,” Hassannia says. “Improvements on the transmit side have been less dramatic, resulting in a 2:1 reduction in size and power consumption.”
“On the LDMOS [laterally diffused metal-oxide semiconductor] side of the equation, we have devices that are moving toward higher level of integration,” Smith says. “RFICs that offer several stages of gain and additional features such as power sense, temperature compensation; it’s in a small plastic package which makes it lighter weight, has higher conductivity in the flange which helps that thermal resistance, and is less expensive than traditional ceramic packages.”
NXP’s entrant in this market, the avionics AFIC10275, “is a silicon LDMOS product: It is a two-stage RFIC designed for transponder applications operating from 978 to 1090 MHz. (Figure 3).
Figure 3: NXP’s AFIC10275N. Photo courtesy of NXP.
![]() |
|
(Click graphic to zoom) |
For UAV developers, “SWaP-C [SWaP plus cost] is still the primary guiding system,” Carlson says. “For example, the communication system can’t be 10 times the platform cost. Clearly whatever communication system or sensor system I put on it, I have to be very cost-conscious. [Efficient transmitter designs are critical] because you don’t want to be throwing away any transmitted RF power, it’s wasted heat,” Carlson says.
RF & microwave benefits communications, radar, EW
The increase in RF and microwave components in UAVs is having a positive effect in delivering to the warfighter the systems they require for successful missions.
“It’s funny, because in a sense, I think [the components] are all a little bit codependent in that a UAV has a great suite of sensors but no ability to communicate that information,” Carlson states, noting that the system then becomes pretty useless if it can’t deliver mission-critical information to the command center.
“Communication links clearly require RF,” Carlson adds. “In general, those links are going to higher and higher frequency for higher and higher bandwidths, so you can push more and more data from the UAV. In other words, there is lot of live sensor data that is not just a command-and-control type of the device, but the idea is to actually get actionable information from the UAV.”
“We see the radar sensors as being an incredibly vital part of the UAVs, as well as of communication links,” he continues. Precision requirements are driving demand for higher and higher frequencies for radar applications, “because as I go to a higher frequency, I can get a much more precise geolocation. Obviously, once I start detecting all this stuff, now I’m in a circular argument. I have to broadcast back so that somebody can actually do something and take action on it.”
For example, MACOM “has a single-chip KU-band T/R module that’s been used in a communication phased array for drones that creates a real-time video link for a military application, providing an over-the-horizon video link,” Carlson explains (Figure 4).
Figure 4: Ku-Band 8 W TRM for radar systems. Photo courtesy of MACOM.
![]() |
|
(Click graphic to zoom) |