Engineering integrity into critical data-rate connectivity
StoryDecember 20, 2018
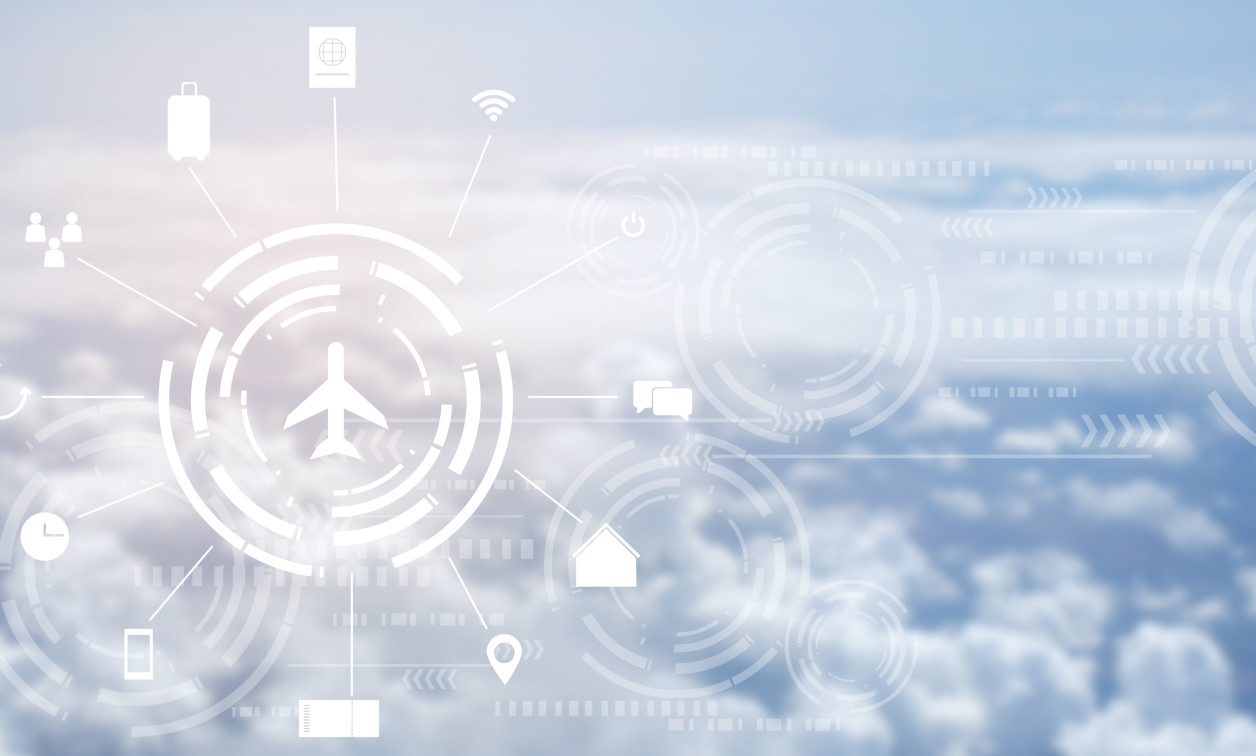
Think about the anxious feeling you get when you’re doing a presentation for an important audience and your laptop freezes. Now imagine you’re a pilot flying above contested territory and relying upon cutting-edge defensive systems to protect your mission, your team, and yourself. Which are the most important components of the system – the sensors, the processors, the displays, or the network of cabling connecting everything? As you peer down upon a missile plume, clearly the answer is all of the above.
Mission Critical
The reality is that we have become highly dependent upon seamless datacom technology to the extent that we trust it to safeguard missions and lives. This trust is not a bad thing, and in a world of emerging threats, it is indeed a necessity. However, as high-tech systems are deployed and continue to evolve, engineering integrity into every link of the system –, including the vital cables connecting embedded electronics – is essential. A lack of signal integrity, often brought about by compromised mechanical integrity through poor installation or post-installation damage, can bring even the most sophisticated system to its knees.
Applications, trends, and economics
As system capabilities grow, data rates are climbing and system density is increasing. Sensor count in both manned and unmanned systems is growing dramatically. Some of this increase is due to the megatrends of automation and electrification, both of which involve the replacement of reliable but heavy mechanical systems with electric alternatives. Some of the mounting number can be ascribed to more sophisticated and higher-resolution sensor systems for situational awareness, including things like persistent wide-area surveillance, which deploys large arrays of sensors. In most cases, any single sensor does not carry overwhelming data requirements, but significant bandwidth and packaging challenges can arise when you aggregate 16, 32, or 96 sensors.
For the designer, the necessity to reduce size, weight, and power (SWaP) remains a primary task. The end user needs that next-generation sensor, but they also need their vehicle to have the same range of operation, be the same size, or still be stealthy, plus it needs to hit the price point. In this context, system value is a significant differentiator. The customer will definitely want to avoid paying 96 times more for the latest array of 96 sensors. The expectation: The system must meet the program’s key metrics and attain higher system functionality with each new generation, thereby maximizing the system functionality-to-cost ratio.
Nice system … will it work and if so for how long?
The situation: Your chief architect has designed the next-generation sensor-intensive system that will take your customer and your company into a new era. Will it work after it’s installed and then for years in situ? Engineering electrical and mechanical reliability into extreme data connectivity is possible, but it is not easy, is not always effectively deployed and can be susceptible to hazards that can arise along the way. High-data-rate connectivity depends on optimized waveguides, which in turn depend upon a variety of material and mechanical attributes, no matter whether the cabling is copper- or fiber-optic based.
The minute a high-data-rate cable – even though designed and simulated to perfection on computer-aided design (CAD) stations – is produced, its ideal performance is under attack. Because no manufacturing process is perfect, material characteristics, geometries, and integration processes all take a toll on ultimate performance.
Integration of the high-data-rate cabling into its platform and application is a tricky area, one that can severely affect its ultimate performance. All kinds of issues during installation – such as outer-jacket damage due to cable-pulling abrasion, distorted geometries due to mounts, repeated flex, overly severe bend radii, and improper shield or conductor termination – can all negatively affect performance.
Damage while deployed – including chafing, pinching, environmental exposure, errant tool impacts, or other human-related damage – can all add up to a cable that superficially appears intact but fails to support intended design-performance levels.
Finally, if all of the technical challenges have been met, will the system support the various stakeholders’ expectations relative to longevity and return on investments by being scalable and upgradable? Most defense agencies are putting forward program requirements mandating open architecture as a baseline for systems involving electronics and optics. This condition sets the stage for enhanced longevity and is usually fundamental to making the original business case. To ease the way, agencies are working hand-in-hand with the defense community and a variety of standards organizations to assure that high-performance open standards are in place as advanced architectures are conceived and deployed.
Good news comes in copper ...
The good news is that aerospace and defense engineers have learned how to ruggedize high-performance wire and cable as the infrastructure of open architecture. They have collaborated with multiple organizations in a broad ecosystem-wide initiative to standardize the most popular physical-layer configurations and are working to fill in missing links of the ever-evolving connectivity chain.
Today it’s pretty common to see 1 gigabit Ethernet (GbE), in the form of a category 5e (Cat5e) or better cable, in defense and aerospace vehicles. Architects are now considering taking the next step in bandwidth, with many exploring and a few already deploying 10 GbE as system functionality, aggregation, and data-rate requirements continue to grow. The 10 GbE (Cat6a) copper solution – an example of which is detailed in Society of Aerospace Engineers (SAE) standard AS6070/5 & /6 – is an easy drop-in replacement for lower-performing varieties of 10 GbE, 1 GbE, and Cat5e. It is approximately the same size and (similar to the 1 GbE cable) has four twisted-pair conductors, but represents a large step forward in signal integrity and data rate. With advanced materials and dual-shielding strategy, this cable variety exists in open architecture form to transparently enable the migration of avionic and vetronic architectures from 1 GbE to 10 GbE. The future of copper continues to be bright, with parallel implementation of 10 GbE channels enabling configurations of 40 GbE, 100 GbE, and higher. (Figure 1.)
Figure 1: Category 6A Ethernet cables.
![]() |
|
(Click graphic to zoom) |
…. and fiber
In box-to-box connectivity applications, many packaging engineers consider 10 GbE as the point to transition from copper-based cable to simplex fiber-optic. As copper functionality continues to be stretched, this is prime trade study territory. Although cost is always a consideration, there are also several performance advantages of fiber that make it very attractive as the ultimate solution: nearly unlimited bandwidth, electromagnetic interference (EMI) immunity, minimal SWaP, and the high availability of standard hardware enabling open architecture. However, some reluctance on the part of systems providers has hampered the deployment of fiber-optic cabling in mission-critical, adverse-environment applications. Thankfully, the latest generation of fiber-optic cabling has proven itself to be highly robust and is alleviating the concerns of the system designers.
A prime example of state-of-the-art simplex fiber-optic cabling finding its way into leading-edge platforms can be found in the standard ARINC 802-2. Supporting open architecture systems, ARINC 802-2 checks all of the boxes for adverse-environment suitability, including wide temperature range, corrosion-resistant construction, incorporation of strength members, and in some varieties the incorporation of crush-resistant features to assure resilience and operational readiness. As a result, mission and flight-critical applications are able to confidently play the fiber-optic card when needed. (Figure 2.)
Figure 2: 1.8 mm simplex fiber-optic cable.
![]() |
|
(Click graphic to zoom) |
Rugged, fast, and ready
Challenges remain for packaging engineers, but highly reliable, extreme-data-rate connectivity is a reality. Cables used in these applications must be designed properly, installed properly, ideally tested after installation, and be treated as sensitive wave guides throughout their intended life cycle. As with the latest generation of embedded electronics, operators and technicians must be trained on the sensitivity of the cables, in order to recognize any damage and call out suspect areas in advance, but today’s high-performance copper- and fiber-based cables have the engineered integrity to enable extreme connectivity in extreme applications.
Gregory Powers is the Global Market Leader, Aerospace & Defense, for W. L. Gore & Associates.
W.L. Gore & Associates • www.gore.com