Powering the future of directed-energy weapons
StoryNovember 20, 2019
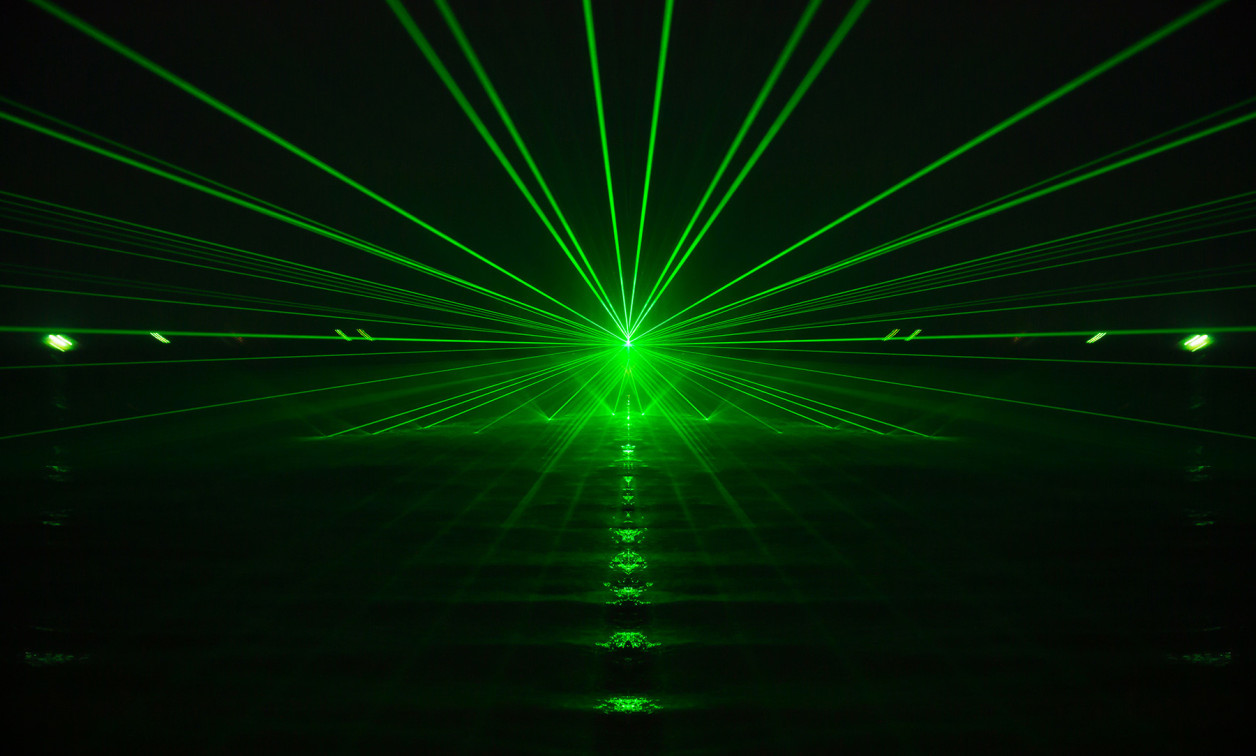
Defense designers face many different challenges in developing directed-energy weaponry, which can employ either laser, particle-beam, or high-power microwave (HPM)/radio frequency (RF) technologies. One feature that these three directed-energy weaponry technology categories have in common is the need for high electric power following implementation of high-voltage solutions. Directed-energy weapon designers benefit by understanding the different challenges that high voltages impose on electrical interconnects and how to solve them.
Continuous- or pulse-power systems are used in directed-energy weapons, along with sophisticated switching and power-conditioning technologies. High-voltage interconnect solutions are needed in these power systems to maximize output energy while minimizing the power impact on the host platform, which may be based on the ground, at sea, and in the air. High-voltage interconnect solutions are employed “outside the box” not only for the energy path connecting the prime power source and energy storage, but also for components that convert energy into the desired output. Today’s directed-energy lasers operate in a range of tens of kilowatts, but designs using hundreds of kilowatts – and even megawatts – is the ultimate objective.
At the beginning of a high-voltage power project, it’s valuable for designers to view interconnects holistically as part of the system. Over the years, specific interconnect products have been introduced – and new technologies continue to be developed – to handle the challenges of high-voltage electric power. For directed-energy weapons applications, designers typically face several power-related issues:
- Managing extreme heat loads: Directed-energy designs must dissipate massive amounts of thermal energy. Keeping the energy source at a safe operating temperature is critical for the safety and efficiency of the system. Although specialized liquid coolers and heat exchangers are employed to transfer heat for rejection outside the system, the interconnects must still be able to withstand internal temperatures as hot as 1,200 °F (650 °C). When a relay is exposed to high temperatures, pickup voltage (VPI) and coil resistance (RC) are affected. To ensure stability, designers need to determine the steady-state characteristics for the temperature and voltage combination of a DC relay’s operating conditions. This is also true for AC applications, although their VPI exhibits less variation over temperature than do DC relays.
- Preventing partial electrical discharge: Managing high power is easier on the ground than in the air. This occurs because high voltage can ionize air, which can become conductive to produce a corona discharge. The corona effect is responsible for electrical power losses through voids, cavities, and electrical treeing as insulation breaks down; electrical arcing is the likely result. Using proper dielectrics and insulating materials is critical to avoiding corona discharges. Insulation using cross-linked polymers for high-voltage wiring, cables, harnesses, and assemblies is formulated to resist breakdown. Using this type of dielectric is especially critical in power-control modules and power converters.
- Avoiding arc tracking damage: Use of high voltage sources in directed-energy weaponry platforms may cause carbon tracks to form on the surface of polymeric insulators, which in turn causes the insulator to lose its dielectric properties and become an electric conductor instead. Electrical arcing can then occur across the conductive path, resulting in power loss with a high probability of ignition. Once again, proper insulation materials must be used to avoid this problem.
- Handling the effects of environment on inception and extinction voltages: Partial discharges can occur when two parts of a circuit that are not adequately isolated from each other are subjected to high voltage differences. Inception voltage is when the corona effect starts; extinction voltage marks when it ends. Consequently, electrical systems must be designed to provide adequate electric isolation levels within the operating environment.
- Negating skin effect: When determining proper shielding and filtering for electromagnetic compatibility (EMC), designers must account for skin effects – the tendency of AC current to flow close to the surface of a conductor. Skin effect is the result of eddy currents induced by the changing magnetic fields of alternating current and is therefore a factor in nearly every AC design. PCB traces and other aspects of AC power circuits can be designed to negate skin effect, but expert planning is required.
- Managing size and weight constraints: Components used in high-power electrical energy storage and management can be large and heavy. High-efficiency relays and contactors are available to handle higher voltage and amperage within a compact footprint, helping reduce size, weight, and power (SWaP) requirements. Specially designed cables, terminations, and connectors are also available to minimize SWaP.
- Higher demand for reliability: The number of open and close cycles can be significant in directed-energy weaponry applications. This extreme cycling puts additional wear on the contact surface of mechanical switches, which must be designed to handle the added stress. For electric switches, proper sizing is needed to handle the required voltage level, because transistors are sensitive to overvoltage.
How to solve these power management issues?
Today’s interconnect products for high-voltage applications benefit from the cross-discipline development of power-management solutions for the automotive, aerospace, energy, and rail sectors. For directed-energy weapons applications, relevant high-voltage technologies include:
- High-voltage relays, contactors, and switches: Advanced, hermetically sealed designs are available that provide an excellent size-to-power ratio and offer voltage ratings up to 70 kV DC and current ratings up to 1,000 amps. Environmentally sealed insulation gaskets are critical for high-voltage applications to minimize intrusion of moisture and contaminants to prevent arcing across the insulator.
- High-performance power feeders and environmental sealing protection products: Cross-linked polymers in advanced heat-shrink tubing and cable accessories can endure repeated heating and cooling cycles while retaining their original size and protective properties.
- Terminals, splices for high temperatures: Terminals, splices, and spare wire caps designed for high-temperature applications can withstand operating environments as hot as 1,200 °F (649 °C).
- Lighter-weight and smaller components: Advanced sealed terminals and splices are available that are 60% lighter than conventional copper terminals, which can help reduce weight.
- MIL-SPEC connectors: The DEUTSCH connector product family includes contacts and connectors, including the MIL-DTL-38999-compliant DEUTSCH connector series. The dielectric withstanding voltage for environmentally sealed DEUTSCH DT connectors offers current leakage less than two milliamps at 1,500 volts AC. (Figure 1.)
Figure 1 | High-voltage, hermetically sealed relays and contactors with a wide temperature range are useful in a variety of directed-energy weapon applications. Image: TE Connectivity.
|
With the range of interconnect products available today for high-voltage applications – and with new products being introduced regularly – directed-energy weapons designers can find reliable and readily available solutions to meet critical requirements. Defense designers who work with experts who can design, customize, manufacture, and implement high-voltage solutions all along the power path can see their directed-energy weaponry projects come to fruition faster.
Franck Kolczak is a solutions marketer for aerospace and defense applications at TE Connectivity, with responsibility for business development for the global defense market for the Aerospace, Defense, & Marine business unit of TE Connectivity. Franck holds a BS in mechanical and electrical engineering from the Ecole Nationale Superieure d’Arts et Metiers (Paris) and an MS in aerospace and astronautics from the Massachusetts Institute of Technology. Over the last 25 years, he has developed a wide range of experience focused on electric systems and interconnectivity applications in various technical and business development functions.
TE Connectivity www.te.com