Innovation in military power supplies: Intelligence, standardization, efficiency
StoryNovember 20, 2019
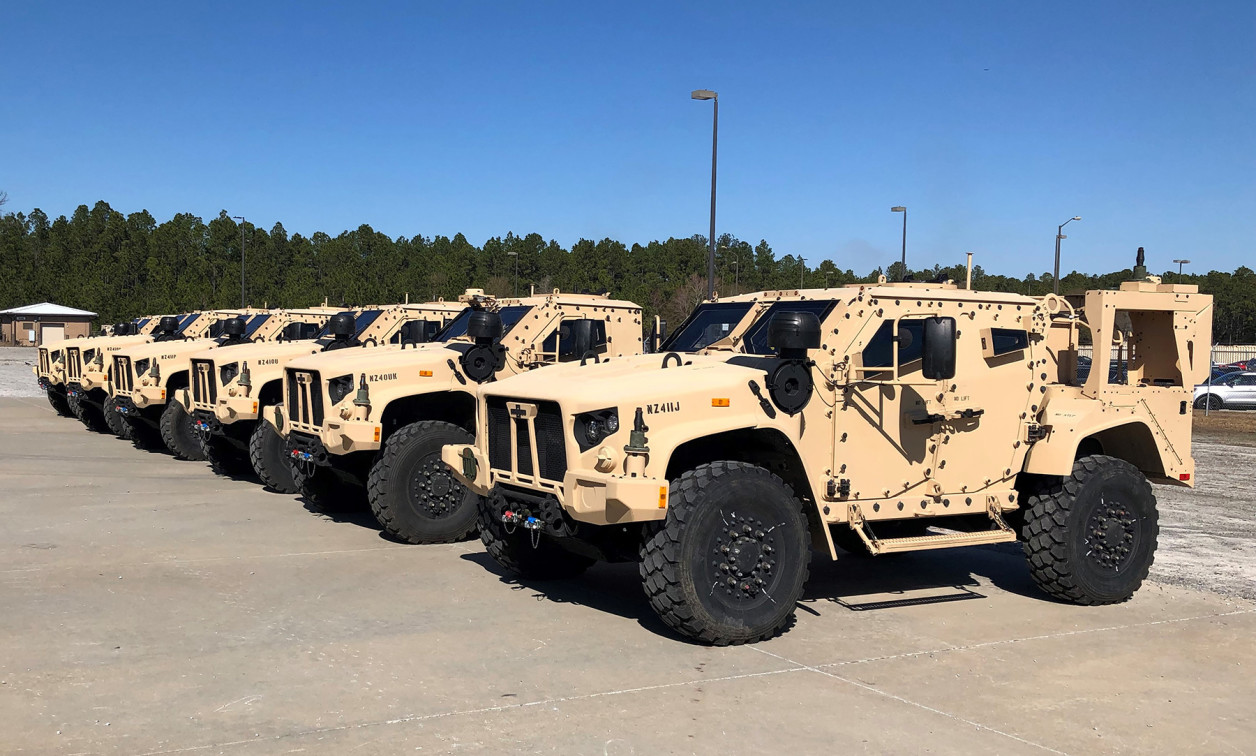
Power-supply designers for military applications face the same reduced cost, size, and weight challenges as other military electronics suppliers. These restrictions can make innovation complicated, but power supply experts innovate nonetheless – in areas like power efficiency, balancing standardization versus customization, intelligent power supplies, and – perhaps most importantly – securing the digital interfaces of modern power supplies.
Reduced size, weight, power, and cost (SWaP-C) requirements define the design of most military electronics today, but SWaP especially influences military power supplies and the companies that manufacture them. When maintaining the form factor, operationality, temperature, and price of a high-voltage power system so that it can meet battlefield needs, the contradicting design requirements become prevalent.
Industry standards like VITA 62, VPX, VME, and CompactPCI (cPCI) have helped manufacturers in the overall design process by implementing formats for the power supplies to follow. However, retaining customizability is still a necessity, and legacy systems are gradually starting to be phased out.
With companies now seeing the advantages of plugging customized systems into standardized power supplies, new capabilities have become simpler to integrate. This has also enabled manufacturers to focus more time and energy on the power supply itself; they are working on power conditioning, power conversion, power utilization, power management, and additional intelligence.
Standardized form factors, commercial off-the-shelf (COTS) electronics, and higher processing power, however, make military power supplies an electromagnetic target. Securing them from electromagnetic interference (EMI) is also becoming something that companies now must consider.
It’s these conflicting design demands that create an endless cycle of “musts” for engineers of military power supplies. What is certain is that the military needs power; what remains in question for manufacturers is how small, how fast, how cool, and how much?
SWaP-C limitations remain a priority
SWaP-C requirements for military power supplies depend on the system that it will be used on. Power supplies for ground-vehicle systems need to be a different size and weight than those for aerial systems, simply because one remains on the ground while the other needs to be lightweight to fly.
“Aerospace and defense customers are continuing and will continue to look to us to help them drive their SWaP-C and improve their SWaP-C performance,” says Robert Russell, vice president of product marketing and power solutions at Vicor Corporation (Andover, Massachusetts). “That particular set of parameters is really what they’re looking to improve, and what we create products around. They’re looking to supplement their C4ISR [command, control, communications, computers, intelligence, surveillance, and reconnaissance] capabilities and all of those things that they want their products to do. But they need more space and weight to do that.”
Taking a modular approach to the design of a power supply is a way to introduce that scalability. As the military introduces new capabilities, it becomes clear that such products will be found in a wide variety of environments and with that comes individual power requirements.
The level of efficiency that modularity could provide may also be a way to make the power supplies easier to cool, which is another paramount requirement when optimizing SWaP-C restrictions. An overall lighter device that can sustain high power while remaining cool is a reality that modular power supplies could offer as designs progress.
“Technology innovations that can be game changers are improvements to power devices, enabling higher-power, efficient, conduction-cooled power supplies,” says Lou Garofolo, product manager, power division at North Atlantic Industries (Bohemia, New York). “An NAI product which has reaped the benefits of such technologies is our VPX56 family of 6U VXPX power supplies. This product started out several years ago as a 700-watt power supply and these type of technology advances have allowed us to double the power in the same size package.” (Figure 1.)
Figure 1 | North Atlantic Industries’ VPX56H2-6 programmable power supply is conduction-cooled through the card edge/wedge lock.
|
Another factor in SWaP-C optimization is the standardization of these power supplies: Having industrywide specifications for manufacturers to meet when designing power supplies for the military could create a level of predictability when size, weight, and temperature con-straints are presented. So much so that, according to industry officials, VPX and VITA standards have slowly began phasing out cult classics like VME and cPCI.
Goodbye VME and cPCI, hello VPX
The level of customizability in a VME power supply is such that each supply is unique to the system it’s operating on. While that can be beneficial for the customer, it could be argued that its individuality is so varied that a “VME supply” doesn’t technically exist. They are truly custom supplies with no standard in their design, so each one is completely different.
“Prior to VPX, Behlman had done lots of VME supplies. But VME never had a standard format. It all depended on the size of the system, there was no standard at all,” says Jerry Hovdestad, Director of COTS Engineering at Behlman Electronics (Hauppauge, New York). “With VPX now, they’ve standardized the size of the supplies. There are standard form factors, there’s standard configurations, 3U and 6U, and there are several different subcategories of the output voltages just to get close to a standard that everyone will use.” (Figure 2.)
Figure 2 | Behlman Electronics’ VPXtra 700D-IQI is a SOSA-aligned, 3U power supply that delivers up to 700 watts of DC power via two outputs.
|
Another benefit of standardizing power supplies is that because they aren’t being designed for an individual military program, the product has already undergone EMI, shock and vibration, and environmental testing. This could reduce time to market and deployment time, getting the product onto the battlefield more quickly.
Taking advantage of a prequalified power supply is something that the government hasn’t really had the option to do until recently, and the Sensor Open Systems Architecture (SOSA) Consortium is trying to narrow the standard even more. This new reality could allow for fewer possibilities for failure and discourage the use of user-defined benefits, while making room for interchangeability and upgradability. But what that could mean for VME and cPCI may be its absorption.
“The VME space has been slowly consolidating over the last couple of decades,” says Scott Lee, director of aerospace and defense sales at Vicor. “At this point, almost everything we’re seeing is VPX-based. We do have parts in the VPX space, but we also do support a lot of other customers in the VME space. A lot of module-level products can be included on their system-level parts.”
Manufacturers agree that while there will always be a demand for VME and cPCI simply because they are supporting numerous successful power supplies that are currently in use, VPX offers competitively fast performance, high speed, and reliable processors. Moreover, demands for power supplies with high voltages that support extensive and fast processing capabilities are gaining prevalence.
Supporting high voltage, high current
Military customers are not only looking for power supplies that can provide higher voltage than in the past, but there also exists the need for a power supply that can reliably distribute it. Aircraft propulsion, for example, requires around 400 volts DC, for example, but there appears to be little in the marketplace capable of both distributing that power and protecting the wiring. (Figure 3.)
Figure 3 | DDC’s 280W IFEC & PED Solution maintains low input harmonics of DO160 over the 360 to 800 Hz input frequency range with a 28 volt output.
|
“We’re seeing a push toward higher power and higher voltage mainly because, whether it be in ground vehicles or aircraft, what we’re seeing is a push toward electric actuation as opposed to traditional mechanical hydraulic actuation,” says John Santini, chief technologist at Data Device Corp. (DDC – Bohemia, New York). “So, we’re seeing the 270 volt bus and the 400 volt DC bus becoming more popular.”
Products like DDC’s solid-state power controller (SSPC) aid in power switching by acting essentially like a circuit breaker. According to the company, digital communication capabilities supplement the circuit-breaker function by sharing information to and from the SSPC to inquire about its status and ideally reduce the need for scheduled maintenance.
With higher voltages, the overarching need is that of combining power supply, circuit protection, and power management all in one. Power supplies that achieve these requirements have a better chance of reducing the number of line-replaceable units on a system, which could in turn save the customer space and weight while giving them a single part number to manage. (Figure 4.)
Figure 4 | Vicor’s family of isolated MIL-COTS modules utilize high-frequency zero-voltage switching topology to achieve power density plus thermal and electrical performance.
|
“Historically, what customers have asked for is more power,” says Michael Agic, business unit manager for power control at DDC. “They say we need high voltage, and we need more current, but now we’ll have to dissipate more. Now we need to cool it off, so now we’re adding weight. Now that it’s heavy, they need more current and voltage. And the cycle just gets worse and worse.”
Manufacturers believe that there is one sure way to manage the side effects of power dissipation, and that is simply to create less of it. Switching technologies like gallium nitrade (GaN) and silicon carbide (SiC) have helped in that regard.
“For typical power supplies, the game changer has been GaN and SiC.” Santini says. “SiC is great because it is typically a high-voltage part, and it’s much faster. You can now switch faster and reduce the size, and ultimately that reduces the cost. We’re looking at the same thing in low voltage on the GaN side.”
Intelligent power supplies and keeping them secure
Embracing the hardening and digitization of power supplies also creates opportunities for implementing intelligence: Power supplies built with the ability to communicate across a bus and run both prognostics and diagnostics, however innovative, present a new set of pros and cons.
“The intelligent power supply will be the most important feature to improve the whole system architecture.” Hovdestad says. “You can have a dual data bus communication where a system controller or chassis manager can talk to the power supply and inquire about input voltages, output cards, power temperatures, and other information from the power supply, possibly predicting failures.”
Conversely, an intelligent power supply would require users to address it digitally, which puts it in a vulnerable electromagnetic position. Not only does it make the power supply registerable on the electromagnetic spectrum, but it could create an easy opportunity for adversaries to attack the communication system.
“Today, everyone wants to be able to address a power supply digitally and to control it. Turn it on, turn it off, turn it up, turn it down. That’s where you get into vulnerabilities, when you build in that kind of digital interface.” Santini says. “We have a number of initiatives in-house where we’re paying attention to cybersecurity and limit exposure. If we do offer communications, it’s limited communications, and we keep the communications path very short and very focused.”
Similar to most military technology, advancements in power supplies will take time and are hugely dependent on military funding. As the battlefield evolves, so will the need for power, how much there’ll be, where it’s directed, and how it should be distributed.