Ruggedizing a commercial enclosure? Not so fast …
StoryAugust 05, 2024
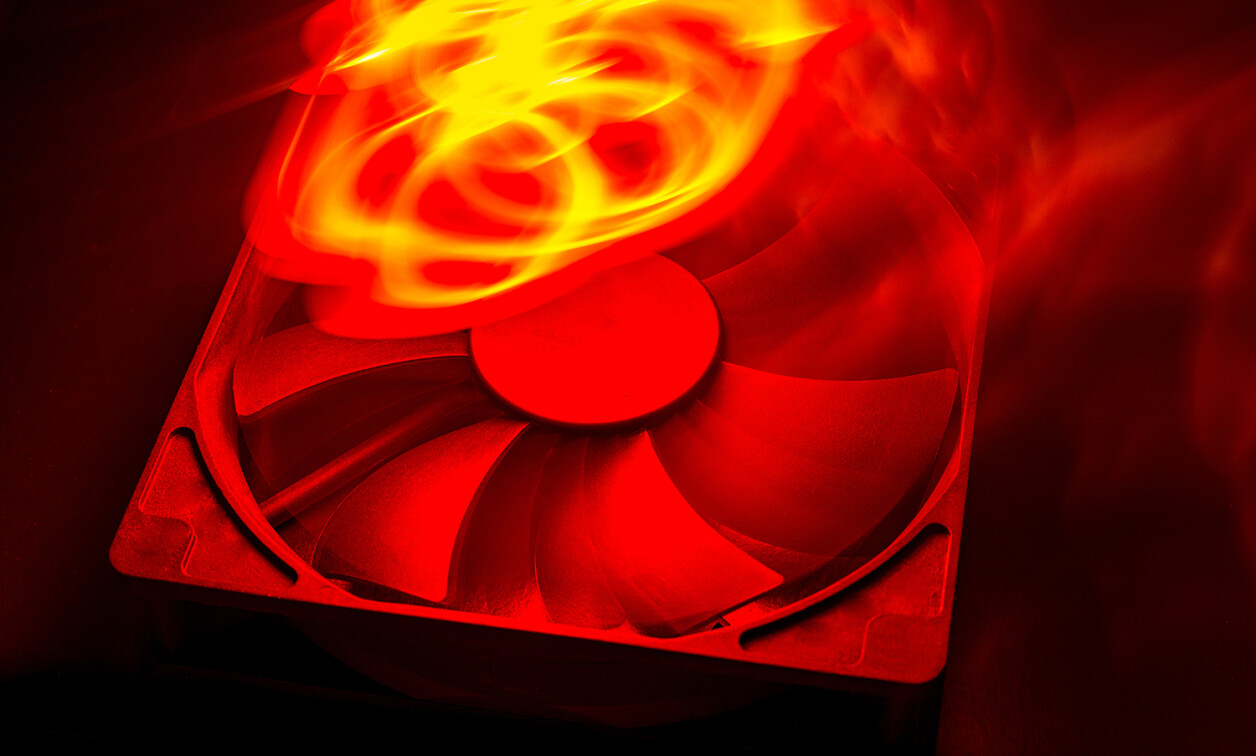
While it is true that board-level embedded products can be extremely difficult to design, designing and/or ruggedizing an enclosure for an embedded computing system carries its own set of challenges.
The enclosure platform for an embedded computing systems is often the Rodney Dangerfield of the industry: “I don’t get no respect” was the catchphrase of the late comedic legend. Often, this is the plight of the chassis manufacturer. The enclosure is commonly an afterthought and at times there is little understanding of the potential complexity of these systems, especially ruggedized designs. This is especially apparent in vendor-specific products such as NI’s (now a part of Emerson) software-defined radios (SDRs).
Open standards versus vendor-specific designs
When it comes to a modular open systems approach (MOSA), such as OpenVPX, there is a family of VITA specifications to follow. It is not just a matter of what is allowed, but what is commonly accepted practice, what gray areas can bring roadblocks, and the “dark art” of backplane design and thermal management.
For vendor-specific designs, the plus side is you often do not need to worry about meeting the specification of an open standard. But, it does require the engineers to understand the performance specifications of a very specific design. In working with a vendor-specific design such as an SDR, it was very beneficial to have the years of expertise in the open standards community. This includes knowing the parameters of cooling, I/O management, ruggedization, typical end-system environments, signal performance, and more. There is certainly a significant task in ensuring that the components you choose to make a system IP67-compliant or full-military rugged do not degrade the signal performance (more than very minor potential losses from altering the interconnect path). This is especially true for RF signals where there is a premium for high performance.
Challenges in ruggedizing commercial-grade SDRs
Perhaps the most important element in ruggedizing a commercial grade computing/RF system, such as an SDR, is the working relationship between the radio vendors and the one creating a hardened solution. First and foremost, to be able to cool the unit, you will need to understand the thermal profile of the provider’s boards. This may include multiple daughtercards. To achieve that, you really need the cooperation of the device’s supplier.
Some of the challenges in ruggedizing the SDRs include providing adequate cooling; ensuring IP67 sealing; meeting the military specifications that may be required; reaching signal performance goals; meeting general size, weight, and power (SWaP) considerations; and much more. Figure 1a shows an example of a commercial SDR, while 1b shows the ruggedized version.
[Figure 1a & 1b ǀ The commercial-grade NI x310 SDR in Figure 1a is designed for lab use, with internal fans for forced-air cooling. A ruggedized version as shown in 1b is often conduction-cooled and IP67-sealed to resist sand, dust, and moisture and to withstand a wider temperature range.]
Cooling is one of the first challenges: In the design example, upon receiving design details from the board vendor, the first step was using thermal-simulation tools to optimize cooling outcomes. As such, we were able to achieve effective cooling in -10 °C to +50 °C grade environments (as high as 10,000 feet) for a conduction-cooled unit that featured a high-performance user programmable Kintex-7 FPGA [field-programmable gate array] with daughtercard options tunable from 10 MHz to 6 GHz with 80 MHz of instantaneous bandwidth per channel. By applying an optional modular design for an external military-grade fan and internal heater, the rugged SDRs can be used in -40 °C to +71 °C operating environments. The fan would need to meet the typical military specifications and blow over the air conduction-cooled external fins, so that no airflow is going inside of the fully sealed unit. Knowing the exact hot spot in the system, the designer can direct the airflow over the hottest part of the chassis.
Of course, the customer’s application always dictates what cooling methods are acceptable. Bottom line: Even a semi-hardened air-cooled version of the SDRs is required for some projects.
Ruggedization levels
In developing ruggedized SDRs, a recurring question often arises from a potential customer, “Do you have something that is more rugged than the commercial box, but not conduction-cooled? The unit would need to be air-cooled.” The problem is that in certain environments, a commercial SDR would not be able to cool the powerful processor enough. Further, the customer often prefers that units meet military transport-grade requirements – essentially being able to survive a hard landing from a C-130, for example. Figure 2 shows an example of a semi-rugged SDR version.
[Figure 2 ǀ Creative solutions can be developed while focusing on resolving another problem. For example, this dual SDR unit that fits in a 1U rack was designed to help improve chassis cooling and a semi-rugged transport grade frame but led to an innovative two-in-one design.]
The two most important points in moving toward ruggedized equipment: thermal-management expertise and applying rugged but cost-effective strengthening methods to metal design. While the above is perhaps the least complicated design from a technical standpoint, it still is not easy to try on your own. Going back to knowing the hot spots from detailed knowledge in working with the board partner, an experienced enclosure designer would be able to concentrate airflow on the hottest spots in the system. Knowing the appropriate fans to utilize in the most effective front-to-rear airflow configuration is another consideration, being careful to avoid air-blocking components. Finally, employing a light but rugged metal design, along with key reinforcement areas, ensures that the unit is properly hardened. Naturally, designing the chassis to meet stringent military standards can add much more complexity.
Testing ruggedized enclosures
Ruggedized enclosures for outdoor use can be designed to protect against moisture, dust, sand, etc., but also extend the temperature range of the systems without an internal fan that would expose the unit to these elements. There are often simple loopback tests where the system is cabled to verify the boards are in working order. While rugged can be designed to support use outdoors, there are military and other applications where it also needs to be strong enough to survive transport, a drop test, seismic activity, shock/vibration from weather, and other military specifications. See Figure 3a and 3b for images of the testing for military specifications for shock/vibration, etc. Balancing the SWaP aspects to a proper cooling and durability level can be tricky, requiring careful application of multiple disciplines. (Figure 3a and 3b.)
[Figure 3a & 3b ǀ These images show the level of testing that is often required to prove that the customized rugged enclosure can meet military-specifications for areas such as shock/vibration, EMI, humidity, temperature levels, and more. Figure 3a shows a shaker table, and Figure 3b shows an environmental chamber. Photos courtesy of NTS.]
For military rugged requirements, the key objective is to meet the specifications of the project. Typically, this includes MIL-810 for shock and vibration, MIL-461 for EMI, and there may be other critical tests as well. These may include DO-160 shock, vibration, and crash safety tests, as well as conducted and radiated emissions, conducted susceptibility, cable bulk injection, power leads, and more.
Finding the best approach
While significant pitfalls were avoided with careful due diligence and testing, there is often a learning curve in finding the optimal approach to serve what may be a wide array of application dynamics. Much like the MOSA designs described earlier, having that experience and learning the art of high-performance RF systems is important.
Justin Moll is vice president, sales and marketing, at Pixus Technologies. He has been a sales and marketing management consultant and senior-level manager for embedded computing companies for more than 20 years. Justin has led various committees in the open standards community and is a regular guest speaker at several industry events. He holds a degree in business administration from University of California, Riverside. Readers may reach the author at justin.moll@pixustechnologies.com.
Pixus Technologies
https://pixustechnologies.com