Rad-hard by design methodology in today’s military and space markets
StoryJune 14, 2023
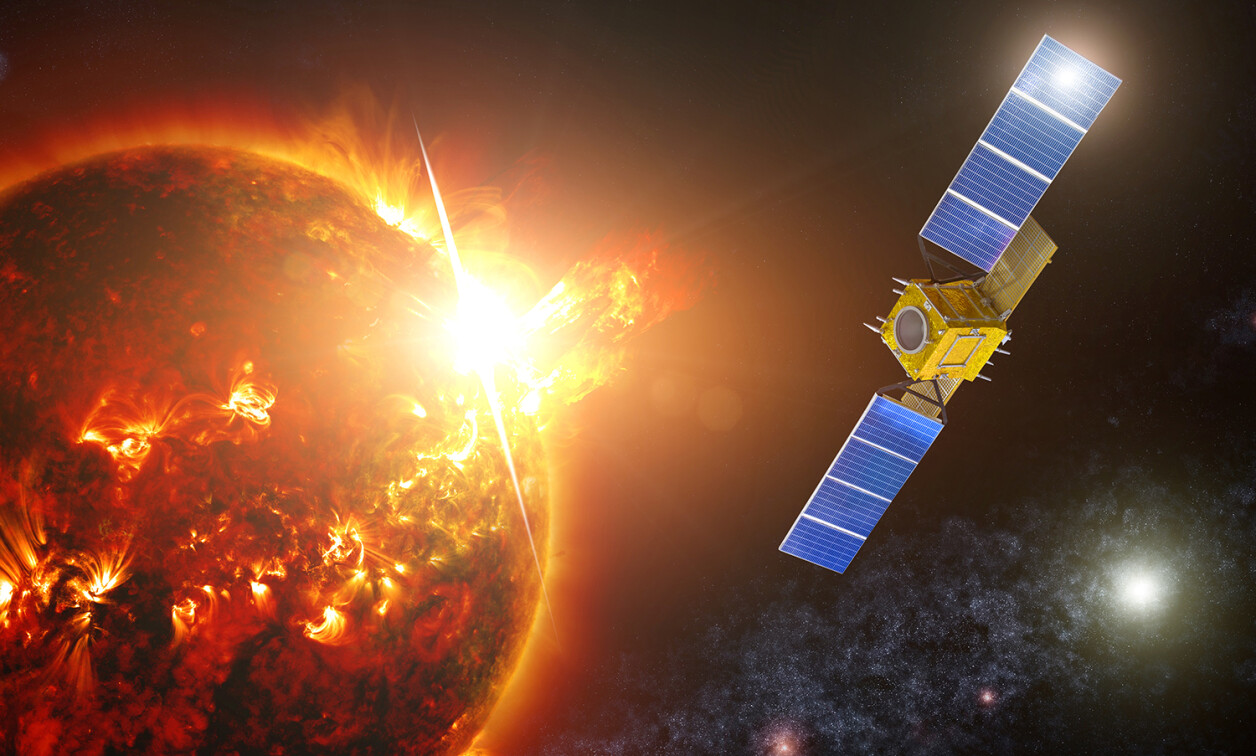
The demand for high-performance electronic components for the space, defense, and nuclear markets in 5G/6G communication, real-time imaging, and nuclear instrumentation is hindered by the limited availability of radiation-hardened (rad-hard) components. Two solutions exist: The first is up-screening commercial off-the-shelf (COTS) components, with the second being the use of space-graded electronics. While the COTS approach is cheaper, it requires expensive risk management and may incur high costs throughout the product life cycle. Rad-hard components are preferred, but are limited to legacy components with high costs that typically do not match COTS performance. A radiation-hardened by design (RHBD) approach can meet performance, availability, and cost requirements.
The current demand in high-performance semiconductors for 5G/6G communication, real-time imaging in defense and space markets, and high radiation-tolerant electronics (>1 MGy or milligray, a unit of absorbed radiation equal to one thousandth of a gray, or 0.1 rad) for nuclear fusion and SMRs is hampered due to limited availability and performance restrictions. While there exist strong growth drivers in the arena, the availability of components is limited, creating obstacles for the industry.
To date, two main solutions exist to utilize electronic components in harsh (radiation-filled) environments:
- Upscreening of commercial off-the-shelf (COTS) components and/or
- Use of space-graded-radiation-hardened electronics.
Using COTS components has the benefit of leveraging the latest technology advancements for new applications, leading to cutting-edge communication and imaging solutions. COTS electronics have been utilized in radiation environments, such as space and high-energy physics experiments, for low-dose applications where rad-hard solutions are unavailable. This usage affects the system’s reliability. Risk management is therefore mandatory and often follows the following procedure:
- Apply sufficient shielding to reduce the level of radiation exposure
- Electronics parts selection through up-screening
- Following strict radiation-hardness-assurance policies
- Extensive radiation testing and understanding the radiation effects on the COTS components
- Apply system-level error detection and correction
- Add system-level redundancy assurance
The whole procedure is costly, and sometimes even inadequate, especially for mission-critical systems where no risk can be tolerated. The threshold for total ionizing dose (TID)-induced failure of CMOS [complementary metal oxide semiconductors] COTS components varies widely. Dose rate effects must of course to be taken into account, because these can significantly change the failure threshold. Typically, most CMOS components can stand dose levels of the order of 5 to 10 krad (1 Gy = 100 rad). Very few of them fail below 3 krad, some can make it to 30-50 krad (0.3-0.5 kGy), and a small minority can survive up to 100 krad (1 kGy). The variability in radiation tolerance is also well-known for COTS components due to variations and imperfections in the chip-manufacturing process. Another element that electronics used in space must endure: high energetic particles, which typically cause single effects; up to certain levels, these events can be prevented by implementing redundancy. However, more severe events – like single-event latchup – can outright destroy components.
Semiconductor vendors produce their components in several manufacturing plants worldwide, and it’s a fact that parts manufactured in different production lines are very likely to have different radiation tolerance. Moreover, as long as the specifications in the datasheet are met, the manufacturer can introduce as many changes as it wishes in the product without ever notifying the customers. Those changes – which could range from changing a few steps in the technology all the way up to a redesign of the circuitry in an accompanying technology – are usually not documented and may change the radiation tolerance.
Another important aspect of rad-hard is the life cycle cost: Initial procurement costs of COTS parts without radiation hardness are less than space- or military-graded parts, but many other factors – for example, added testing, characterization, markings, binning, etc. – will determine whether the cost of ownership over the life of the system is actually reduced.
Life cycle costs are also impacted by part obsolescence: As COTS suppliers constantly introduce new products, previously introduced devices can become obsolete even within the planned product life cycle, which can place a critical or strategic application at risk.
Bottom line: While use of COTS components is possible in some nonextreme cases or noncritical systems, extreme caution must be taken to limit the risks of system failure. Moreover, life cycle costs should be considered, as a price hike during the systems’ lifetime could exceed the cost of a rad-hard component.
Those who go with solution number two – space-graded rad-hard electronics – will find limitations on the availability of the components, electronic functions, and use of legacy components, which typically cannot match the performance of available state-of-the-art off-the-shelf components.
Radiation-hardened integrated circuits (ICs) are available from a range of players – including TI, Analog Devices, ST, Honeywell, etc. – but the ICs offered by the majority of these players are only qualified to radiation doses of <10 kGy and are typically created in legacy processes that cannot withstand harsh environments or with older design methodologies. At the same time, components are expensive and may not even meet the power requirements or electronic specifications of COTS components available on the market.
Radiation-hardened components used in space and military applications need to withstand severe radiation effects caused by energetic particles such as electrons, protons and heavy ions. The radiation environment in space is very different from the civil nuclear radiation environment, where total-ionizing-dose level is much lower (typically below 10 kGy), but particle energy level is much higher (> 100 MeV). Therefore, space-grade electronic components are also designed with a TID tolerance of typically not more than 10 kGy. Using space-grade components in nuclear applications where the accumulated radiation exceeds 100 kGy – and can reach up to 1 MGy and higher – will require designers to take a similar approach as those who use COTS components.
In the nuclear industry, space-grade electronics can only be used in these high-dose radioactive environments with the addition of heavy shielding, which leads to bulky solutions, making the design and installation of complex sensing and motion-control systems an impossible task. Such a situation – large-footprint systems – is untenable in the space environment, where small is better.
What’s needed: components that can both withstand high radiation tolerance (>1 MGy) and meet the reliability requirements of space and military markets, while at the same reaching performance levels of COTS components.
Such an approach requires the use of more advanced technology nodes available at commercial foundries worldwide, which is possible by creating semiconductors that are created by radiation-hardening by design (RHBD) methodologies (Figure 1) through characterization of technology nodes and sophisticated modeling of transistors.
[Figure 1 ǀ A diagram shows an example of a radiation-hardened-by-design workflow.]
Today’s MGy radiation-tolerant integrated chips created through RHBD methodologies enable complex remote handling, automation, and predictive maintenance applications in high-radiation nuclear environments such as nuclear fusion and new reactor technologies.
In the same way, the space industry needs to use a method that ensures electronics in the radiation environment of space are resistant to damage yet remain compact, miniaturized, and high-performance. These demands are driven by the major incentive of reducing the average cost of satellites to enable construction of mega constellations.
RHBD methodologies can enable the development of highly integrated system-on-chip solutions by using advanced semiconductor processes used to develop current COTS components. This approach can reduce mass and power consumption, improve performance, and ensure reliability.
In other words, RHBD is a door-opener to applications requiring extremely high-dose-tolerant ICs while at the same time meeting the demanding electronic and reliability performance guidelines of the military and space industries.
Jens Verbeeck is an electronics engineer with a diverse range of experience in both academia and industry. He holds a master’s degree in electronics and began his professional career at Intersoft Electronics as an electronic hardware engineer. Later, he pursued a Ph.D. in electrical engineering from KU Leuven (Belgium). His research focused on mixed-signal ICs that tolerate increased temperatures and megagray radiation. This work led him to co-found (with Dr. Ying Cao) Magics Technologies, which specializes in radiation-hardened semiconductors.
Magics Technologies • https://www.magics.tech/