Naval electronics face rugged application challenges
StoryAugust 05, 2024
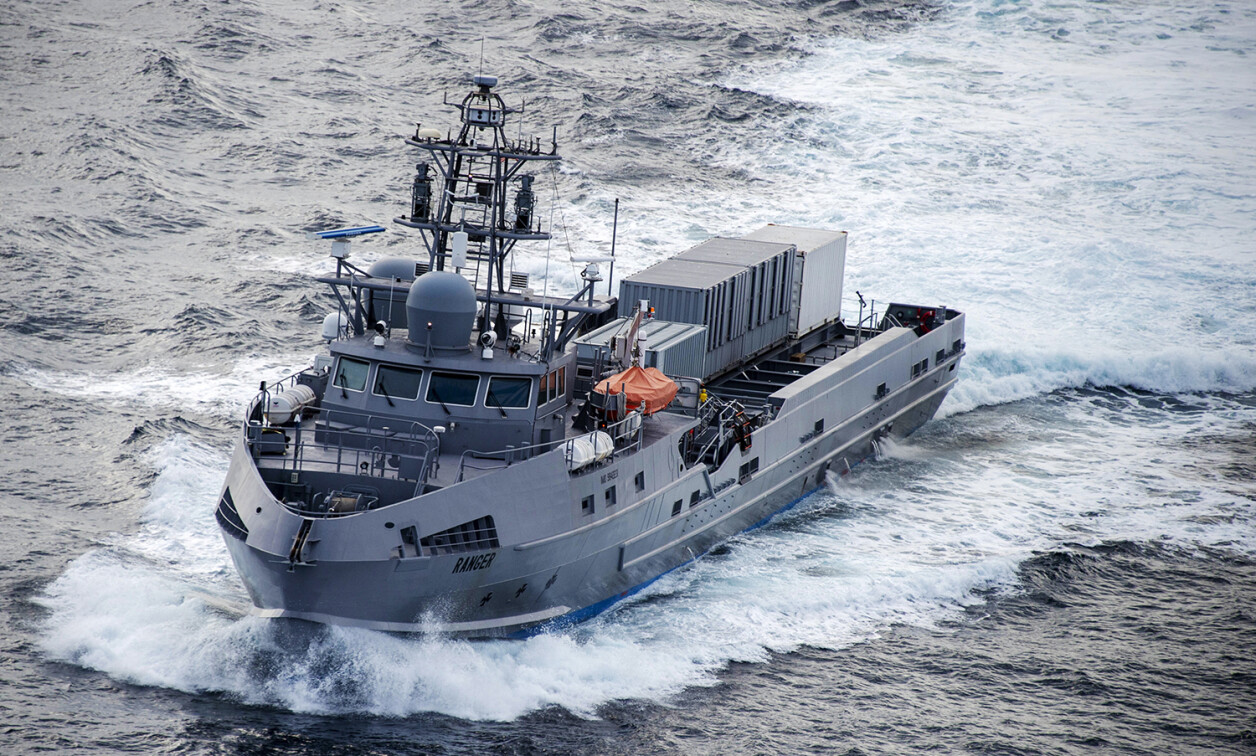
Advanced electronics are central to the readiness of any modern naval vessel. From mission-critical applications such as targeting, radar, and communications to basic functional monitoring and controls, the electronic infrastructure of marine vessels must remain in working order through long deployments in some of the harshest environments on the planet.
Protecting sensitive electronic equipment can present a significant challenge to naval design engineers. A wide range of environmental factors must be considered and mitigated when selecting appropriate enclosures for marine electronics. These factors can be broken down into three main categories: mechanical considerations, electrical and electromagnetic considerations, and environmental considerations. Designers also face the same routine challenges found in land-based electronics applications, including physical access control, thermal management, power distribution, and cable routing and organization. While every application is unique, there are some common ways to overcome these obstacles and ensure that critical naval electronic systems are protected and available around the clock.
Standards for shipboard equipment
The U.S. Department of Defense (DoD) maintains a comprehensive list of standards for equipment deployed in military applications. By selecting equipment qualified to these standards, design engineers can ensure COTS [commercial off-the-shelf] solutions already meet the minimum requirements to protect critical systems. Several standards directly address challenges found in shipboard electronic applications and are often referenced when designing enclosures for naval vessels:
- MIL-DTL-901E: This standard replaces MIL-S-901D, which was the DoD standard for mechanical shock testing from 1989 to 2017. The new 901E standard specifies test criteria for high-impact shock testing to ensure that enclosures can withstand harsh naval operation and naval combat environments, protecting mission-critical equipment when reliability is most needed. One key addition to 901E is the inclusion of a new “Deck Simulating Shock Test” in addition to the mechanical shock and impact and live ordinance barge testing specified in 901D.
- MIL-STD-167-1A: Mechanical vibration testing for shipboard equipment ensures the enclosure and electronics within operate reliably while experiencing vibration from common naval sources, including engine vibration across a range of frequencies.
- MIL-STD-461G: EMC [electromagnetic compatibility] testing ensures that the enclosure provides protection against external EMI [electromagnetic interference] as well as effective containment of emissions generated within the cabinet. Radiated and line emissions have the potential to transmit data that can be intercepted and exploited by adversaries, making effective electrical shielding imperative for sensitive communications equipment. In some applications, protection beyond MIL-STD-461G is required, up to and including TEMPEST-level signal protection (the U.S. government specification for protecting against data theft through the interception of electromagnetic radiation).
MIL-STD-810E: Salt fog testing provides peace of mind that equipment inside the enclosure will be protected from potentially harmful corrosion caused by exposure to saline air during long deployments at sea. While enclosures located on upper decks are most often exposed to sea spray and rain, and must be appropriately housed in weather-proof enclosures, electronics located below deck can also be compromised by exposure to atmospheric salt. Specifying below deck enclosures tested to 810E salt fog requirements ensures that critical electronics will not be exposed to salinity present in the ship’s ambient air. (Figure 1.)
[Figure 1 ǀ Salt fog testing ensures that equipment inside an enclosure will not malfunction due to corrosion from sea spray and salt. U.S. Navy photo.]
In addition to the standards listed above, DoD publishes dozens of standards addressing specific environmental conditions in shipboard applications. As every application is different, it is critical to specify compliance to a complete range of standards that address the unique requirements of a given installation.
Every application is unique
Standard testing can help provide peace of mind that common hazards have been considered in the design of an electronics enclosure. However, very few shipboard applications are identical, and standards can’t address every possible condition a ship may encounter. In addition to specifying enclosures that meet the tests above, design engineers can benefit from solutions that are modular, scalable, and customizable, but based on a common platform architecture. This ensures that COTS components are readily available while still allowing an enclosure to be modified to meet specific application needs. Common electronics enclosure modifications include:
- Custom vibration dampening and isolation
- Modified I/O and cable entry panels
- Active and passive cooling solutions
- Ruggedized power distribution
- Physical and electronic access control systems
- TEMPEST certification for sensitive communications
- EMC shielding
- Fire-suppression systems
- Cable management and organization
Many of these unique application requirements call for specialized engineering during the design process to ensure the reliability of electronics in harsh conditions. A finite element analysis should be performed for all enclosures mounted on vibration isolators to ensure reliable performance and appropriate tolerances under stress.
Advanced thermal modeling is becoming increasingly necessary to ensure proper cooling of electronics as more computing power is being deployed in the space-constrained applications. Even simple considerations such as the bend radius clearance for cables inside the enclosure can cause significant installation problems if overlooked during the design process.
Because every application is unique, starting with an easily modified COTS enclosure platform can reduce redesign time and improve supply chain resilience, while increasing confidence that electronics are prepared for any environment the vessel encounters at sea.
Installing robust thermal management
In addition to the physical and environmental requirements addressed by MIL standards, modern electronics cabinets require robust thermal management systems. The implementation of advanced vision and targeting systems, autonomous platforms, artificial intelligence (AI), and advanced electronic warfare (EW) systems in defense requires high speed, high availability computing hardware. This generates significant heat, often at higher densities that in the past. (Figure 2.)
[Figure 2 ǀ Naval electronics must rely on different kinds of cooling systems to successfully operate on board.]
Traditional cooling methods such as convection and forced air are often insufficient to handle this increased thermal load. Designers increasingly need to rely on a full suite of cooling systems, from convection to liquid cooling, to successfully run modern naval electronics:
- Convection: Suitable for cooling up to 800 W per rack, depending on ambient air temperature. Requires louvers or perforations to allow airflow into and out of the cabinet. Hot exhaust air must be vented away from the computer room or actively cooled. Works best in combination with a computer room air conditioner to cool the ambient air and monitor environmental conditions.
- Forced air: Suitable for cooling up to 2,000 W per rack, depending on ambient air temperature. Requires louvers or perforations to allow airflow into and out of the cabinet. Hot exhaust air must be vented away from the computer room or actively cooled. Works best in combination with a computer-room air conditioner to cool the ambient air and monitor environmental conditions.
- Air conditioners: Suitable for cooling up to 2,600 W per rack. Best for applications where the ambient air is not actively cooled or is inconsistent in temperature. The hot air exhaust from the air conditioner must be vented away from the computer room/rack.
- Liquid cooling: Suitable for cooling up to 45,000 W (45 kW) per rack. Liquid cooling can enable extremely high computing density per rack, optimizing space in the computer room and reducing the number of racks required on a vessel. Cold ambient air is not required, and the system can operate as a closed loop in a sealed cabinet. Cool water is required from the ship to act as coolant in the air to water heat exchanger. (Figure 3.)
[Figure 3 ǀ A fully enclosed liquid cooling cabinet like the CP LHX + is suitable for applications involving complex testing situations and multiple sensors. Image courtesy nVent Schroff.]
Quality and compliance
A final consideration is ensuring compliance to DFARS sourcing requirements and project flow downs; DFARS [Defense Federal Acquisition Regulation Supplement] compliance is a set of cybersecurity regulations that defense contractors and suppliers must follow in order to be awarded new DoD contracts. When selecting a supplier partner for naval electronics infrastructure, it is critical to ensure that all relevant quality and sourcing requirements can be met. Common supplier considerations in the naval electronics market include:
- Compliance to DFARS material traceability requirements
- International Traffic in Arms Regulation (ITAR) certification
- ISO and AS9100 quality certifications
- A robust counterfeit-parts prevention program
- First article inspection procedures
- A life cycle management program ensuring that once specified, equipment will be available and supported for the lifetime of a program
Going forward
Ensuring the reliability and availability of shipboard electronic systems is critical to naval readiness. While every application is unique, there are several ways that design engineers can address common mechanical, electrical/electromagnetic, and environmental challenges when specifying electronics enclosures for naval vessels. Ensuring that equipment racks meet relevant military and government specifications, have been analyzed for physical and thermal performance, are customized to the application’s unique requirements, and are sourced from a supplier with robust quality controls and experience delivering military electronics solutions all deliver peace of mind that mission-critical electronics equipment can withstand the harshest naval applications.
Matthew Tarney is the Global Vertical Growth Leader for Aerospace & Defense at nVent SCHROFF. In this role he is focused heavily on advanced computing infrastructure for the aerospace, defense, and test and measurement markets. Readers may email the author at Matthew.Tarney@nvent.com.
nVent SCHROFF https://schroff.nvent.com/en-us/