GUEST BLOG: GaAs and GaN MMICs: Key component of defense RF electronic systems
BlogJuly 21, 2023
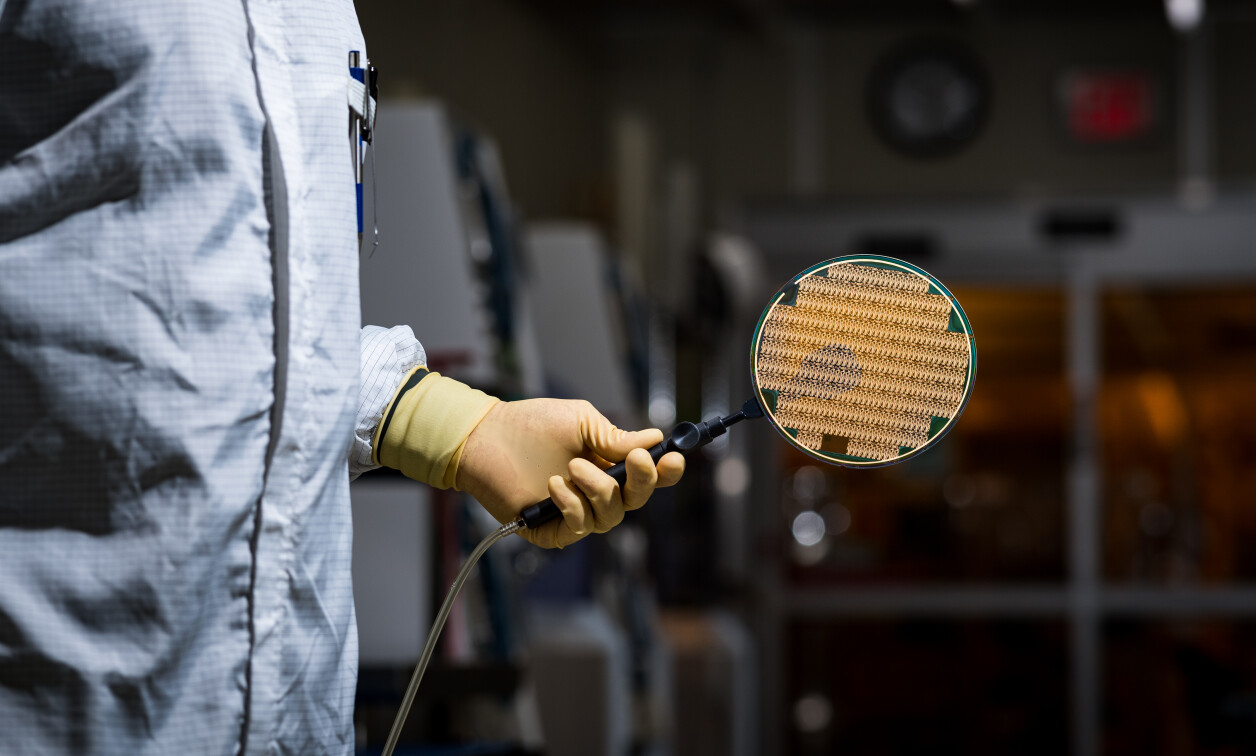
Monolithic microwave integrated circuits (MMICs) fabricated using compound semiconductors are a critical component of a multitude of RF [radio-frequency] systems. For commercial wireless applications, gallium arsenide (GaAs)-based power amplifiers are ubiquitous in the smartphone market, while gallium nitride (GaN) products service wireless base stations, SATCOM terminals, and are a core enabler of 5G systems.
Defense systems for radar, missile seekers, electronic warfare (EW), and communications also depend on MMIC products to obtain performance that is not achievable with silicon-based electronics alone. In order to achieve demanding performance requirements, the defense industry leverages advanced devices based on high electron mobility transistors (HEMTs). These devices offer the best combination of high-frequency operation, low noise, high linearity, and high output power density of any semiconductor technology.
GaAs HEMT products emerged in the 1980s and 1990s, and are now well established in RF systems, whereas GaN HEMTs are a newer technology whose use is rapidly expanding. Designers may want to consider GaN because the transistors produce approximately five times the power density than the incumbent GaAs devices. This aspect of GaN now means that solid-state power amplifiers (SSPAs) based on GaN MMICs are replacing legacy traveling wave tube amplifiers in many radar and EW systems. Both GaAs and GaN technologies are pushing towards advanced process nodes with higher operating frequencies and higher efficiencies in order to achieve better performance and enable dominance over a broader range of the RF spectrum.
The BAE Systems Microelectronics Center (MEC) is a U.S. Department of Defense (DoD) trusted foundry located in Nashua, New Hampshire, dedicated to producing custom GaAs and GaN circuits. The 70,000-square-foot MEC facility includes the wafer foundry, on-wafer RF testing, wafer dicing, inspection, post processing, microwave module prototyping facility, and production factory for microwave power amplifier modules that use GaN MMICs.
One unique aspect of our foundry is the 6-inch wafer line, which offers higher product yield and lower chip cost compared to the industry standard 4-inch wafer diameter. The MEC’s 6-inch wafer processing line has been running production GaAs processes since 2004, and BAE Systems’ first six-inch GaN MMIC was reported in 2014. In testing, 6-inch GaN wafer processes demonstrated high yield, and excellent performance and reliability, with an MTTF [mean time to failure] of more than 10⁷ hours at 200 °C channel temperature. In progress at the MEC is a “Foundry Modernization Initiative,” a multiyear project to add wafer capacity to the facility, enabling us to keep pace with the growing demand within the DoD and industry for advanced RF MMIC components.
The BAE Systems workhorse production GaN process today is a 180 nm “no field plate” technology that targets broadband EW applications up to 20 GHz. In 2018, the company signed a cooperative agreement with Air Force Research Laboratory (AFRL) to transfer an advanced, high-performance 140 nm GaN process developed by AFRL’s research fabrication facility to BAE’s production-focused foundry. This new process with shorter gate length and superior transistor performance targets applications at mm-wave frequencies up to 50 GHz. Through this “lab to fab” collaboration model, we were successfully able to transition the process, and demonstrate state-of-the-art performance on the 6-inch production line. The 140 nm GaN technology – which will be fully qualified for production in 2023 – represents the DoD’s only 6-inch process at this advanced technology node.
Even more advanced GaAs and GaN MMIC technologies are on the horizon: BAE Systems’ R&D organization, FAST Labs, acts as a trusted partner with government R&D organizations and continues to drive towards higher-performance process nodes. The next GaAs technology has a 70 nm gate length and targets low-noise applications up to 100 GHz where low noise figure, high linearity, and low DC power consumption are critical performance parameters. This technology is the shortest gate length GaAs pseudomorphic HEMT process on the market, and is an excellent alternative to InP [indium phosphide] HEMT technologies because of the low production cost on 6-inch wafer diameter. BAE Systems has already delivered prototype quantities of chips using this process, and it is scheduled to be fully qualified by 2024.
The next GaN technology under development is a 90 nm HEMT process that leverages advanced process features including T-gates and low-resistance ohmic contacts fabricated using n+ GaN regrowth by molecular beam epitaxy (MBE). This process primarily targets power amplifier applications at W-band frequencies (75 to 110 GHz); W-band frequencies encompass a local minima in the atmospheric absorption spectra, so it’s expected that this portion of the electromagnetic spectrum will be exploited by radars, missile seekers, SAR [synthetic aperture radar] imaging, E-band radio, and 6G applications. The proliferation of RF components at this frequency band in the near term will drive the DoD to seek access to the best high-frequency GaN technology in order to maintain dominance over the electromagnetic spectrum. In addition to high-frequency power amplifiers, 90 nm GaN also is useful as an ultrahigh linearity mm wave LNA [low-noise amplifier] or within a monolithic, mm wave transceiver chip.
Dr. David F. Brown is currently the product lead at BAE Systems Inc. for RF MMIC and solid-state amplifier technologies.
BAE Systems · https://www.baesystems.com/en/home