Powering SpaceVPX systems – How to implement efficient standards-compliant solutions faster
StoryDecember 02, 2021
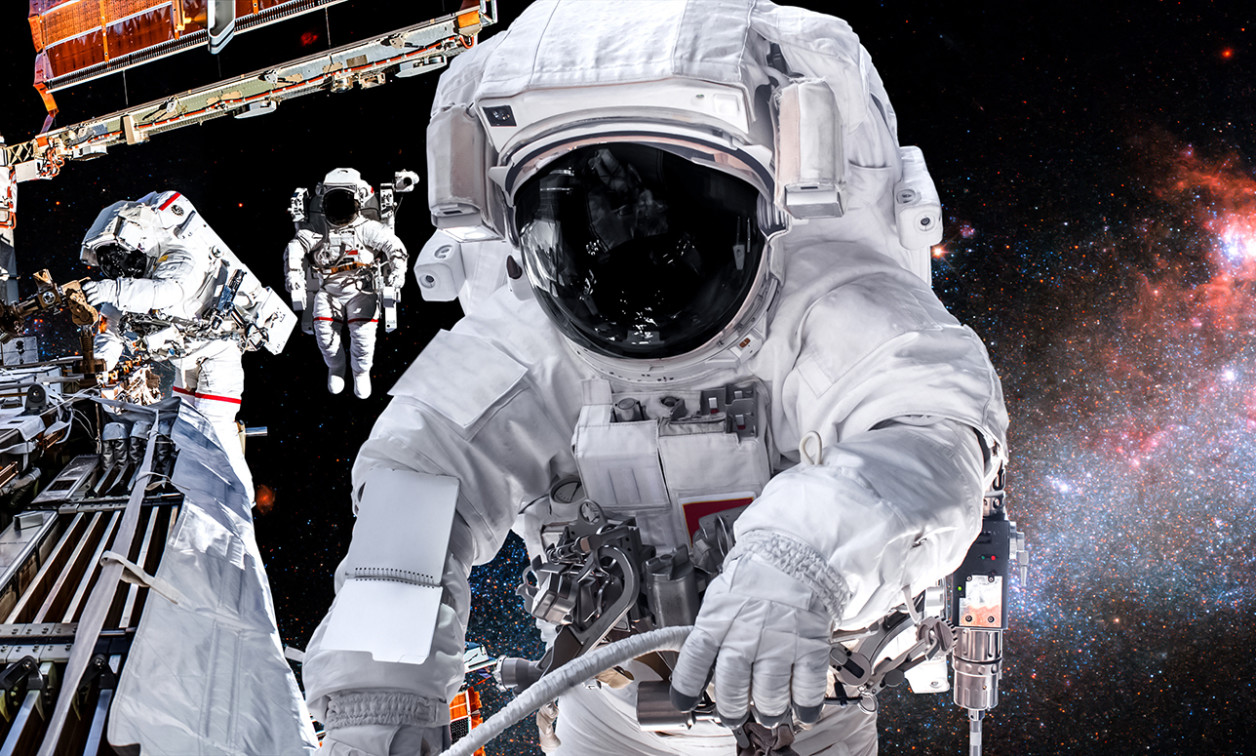
SpaceVPX undertakes a lot to deliver a lot: With so many profiles and configurations available, the devil is in the details when it comes to producing efficient, standards-compliant, power solutions. Supplying and muxing manifold power rails to payload slots through SpaceUM [utility module] is especially challenging due to the myriad of profile choices available and is further complicated in the smaller 3U form factor. The good news is that new, efficient space-grade power-conversion and control technology is making SpaceVPX/UM standards-compliant power supplies and power distribution more manageable, even in the small 3U form factor.
Spacecraft have generationally been typified by architectures built around proprietary systems and design approaches. While serving the needs of the individual program, the custom nature of proprietary implementations tends to be inefficient, costly, and risk-prone. Further, the inherently narrow focus of custom implementations precludes enablement of modularity, interoperability, and upgradability for future systems.
Recognizing the limitations associated with perpetuating custom systems and architectures, many cross-industry consortia and standards groups have come together to develop and promote open system standards like OpenVPX (VITA 65.x), SpaceVPX (VITA 78.0), and streamlined versions such as SpaceVPX-Lite (VITA 78.1). To further refine and encourage standards adoption, groups including The Open Group’s Sensor Open System Architecture (SOSA) and Future Airborne Capability Environment (FACE), along with the Space Power Consortium (SPC), now work collaboratively to establish interoperable reference-design architectures and promote the use of modular and open system frameworks.
Through increased adoption and deployment of standards-based systems, programs benefit from reduced schedules, lower costs, and less risk by reusing proven technology. Further, such approaches are pathways to upward scalability and interoperability and they also build in motivation for commercial solutions providers to innovate and provide relevant and competitive technologies. Let’s take SpaceVPX (VITA 78.0) as a contextual example for open modular systems of particular interest to the space community: What are the power-supply, distribution, and system-management challenges facing developers? Moreover, how is new purpose-built technology speeding the design of systems, with less risk, while adding greater functionality and capability?
SpaceVPX system: a bird’s eye view
Beginning with the OpenVPX (VITA 65.0) standard, the SpaceVPX approach leverages redundancy and cross-strapping with single point-point connections to derive a highly fault-tolerant, high-performance computing platform for space applications. While single-point failure immunity is especially attractive for space missions, its implementation quickly becomes complex and component-intensive, especially when the system is architected to maximize availability of the manifold resources and capability defined by the standard. For perspective, Figure 1 is a high-level diagram of the generalized SpaceVPX architecture interfaced to the Space Power Consortium’s Satellite Power Architecture (which is beyond the scope of this article – learn more at https://spacepower.org/).
[Figure 1 | Pictured is a SpaceVPX system high-level block diagram.]
SpaceVPX platforms are principally comprised of six distinct elements. These elements are the chassis, the backplane, two independent power supplies, two independent system controllers (chassis managers), SpaceUM [utility module] selection and distribution hub, and two 16-payload cards. The SpaceVPX chassis may be implemented in a 6U or smaller 3U form factor with sufficient slotting to accommodate the plug-in elements in a redundant fashion.
SpaceVPX system power supply units (PSUs) receive external power from the satellite power bus or other specific architecture-defined voltage domain. Each power supply is responsible for generating as many as seven voltage rails: +12V/VS1, +12V/AUX, +3.3V/VS2, +3.3V/AUX, +5V/VS3, -12V/AUX, and VBAT. The SpaceUM receives all voltage rails, selects between primary or redundant supplies, and distributes the power independently to each payload slot per the system configuration and controller mandate.
While this may appear straightforward, technology capable of performing this “power cross-point switching” is limited for space applications. Similar to the SpaceVPX power supply distribution architecture, the system controller sources all management and communication signals across the SpaceVPX chassis via the SpaceUM entity.
While power-distribution responsibilities are in themselves a challenge, the point-to-point fan out and buffering of system-management signals – including I2C-based intelligent platform management interface (IPMI), clocks, resets, and selection controls – are left to the SpaceUM module to manage and distribute. This approach appears logical and even tidy, but levies a high demand on the SpaceUM and requires size, weight, and power (SWaP)-optimized components to be successful.
With expanded payload slot card configurations, distributing power and control signals imposes increased complexity and challenges associated with implementing a compatible backplane. This burden is further complicated by the plethora of slot profiles available in the VITA 78.0 standard. The number of permutations makes it difficult for suppliers to efficiently and confidently invest in the development of standard off-the-shelf solutions to support SpaceVPX applications. This is where organizations like SOSA are adding extra value by promoting a narrowed set of reference architectures, thereby reducing and simplifying the number of recommended permutations and associated requirements needed to implement a VPX-compliant system.
SpaceVPX power supply
As the lifeblood of the SpaceVPX platform, the power supply is tasked with converting input power from external voltage source(s) and efficiently delivering multiple voltage rails that may have hundreds of watts of power. While military applications have access to a wide range of efficient, high-power technologies, the space environment is currently more limited. Figure 2 depicts a high-level block diagram for a full-featured, non-SOSA aligned SpaceVPX power supply.
[Figure 2 | Pictured is a 500 W SpaceVPX power supply high-level block diagram.]
Figure 2’s main functional blocks include input power supply conditioning in the form of EMI [electromagnetic interference] filtering and transient protection that provide a clean input for the power conversion and management electronics local to the SpaceVPX PSU. The input supply feeds as many as six isolated DC/DC converters to generate the output voltage rails and a local 3.3V voltage domain to power internal electronics elements – specifically, the microcontroller that manages the output regulators plus reporting status and telemetry to the SpaceVPX system controller.
Consider packing all this functionality into a 3U form factor. It is generally accepted that a 160 mm by 100 mm 3U form factor provides approximately 11,500 mm2 of useable area. Providing an allowance of 1,500 mm2 for the input power conditioning, local 3.3 V regulation and microcontroller leaves 10,000 mm2 of available area to implement the six isolated power supplies to the SpaceVPX system. Thus, to achieve 500 W of power in a 10,000 mm2 area requires an average 50 mW/mm2 power density.
A survey of space-assured isolated converters shows best-in-class power density of approx. 40 mW/mm2, which is insufficient to practically power all six rails described in Figure 2. Additionally, the average efficiency of space-based isolated converters is 85%, which translates to a thermal power dissipation of 75 W for a 500 W supply, a significant amount of heat to dissipate. Consequently, a number of trade-offs would be necessary to create a full-featured SpaceVPX power supply. These trade-offs may have traditionally required reducing the power requirements to something more manageable (like 300 W or less), reducing the number of power rails, or using multistage conversion with a combination of isolated and nonisolated voltage conversion/regulation.
Recognizing these challenges, SOSA and other industry working groups are seeking to refine the SpaceVPX requirements, simplifying its implementation and facilitating configurations that are more aligned to the availability of space capable technologies. Figure 3 depicts a 300W SOSA aligned SpaceVPX power supply, which uses this updated design approach.
[Figure 3 | Pictured is a SOSA aligned 300 W SpaceVPX power supply high-level block diagram.]
By employing only two power supply outputs and lower overall total power, the SOSA aligned configuration lends itself to a simpler, SWaP- and cost-friendly implementation that can be built with existing or near-term space grade components. As shown in Figure 3, a small-form-factor, low-power microcontroller and isolated gallium nitride (GaN) converter is able to deliver 75 W of power, at >91% efficiency, in a 2,400 mm2 footprint. The high efficiency and reduced size of these converters makes SpaceVPX power solutions more efficient, easier to design, and cool. For scalability, each converter can be paralleled with a second device to double output power. Additional design maneuverability will soon be possible, as new 3.3 V and 12 V GaN converters become available that have even higher efficiencies and power densities.
The improved efficiency and power density of the GaN converter topology greatly reduces the challenges associated with heat generation compared with traditional space-borne solutions and is small enough to fit within the 3U SpaceVPX power-supply profile. Taken together, these radiation-hardened building blocks are enabling practical SOSA aligned SpaceVPX power-supply solutions to be quickly produced. Having solved and met the power conversion requirements, the next functional SpaceVPX block to be addressed is the SpaceUM.
SpaceUM power distribution and system management fan out
Let’s go back to Figure 1: The SpaceUM receives the power-supply rails and system-management signals, then assumes the responsibility of selecting/distributing each power-supply rail to all payload slots in addition to fanning out and buffering the system-management signals. In principle, this is a logical approach; but in practice it is not so simple, given the limited availability of power-switching electronics and signal-routing solutions available to space engineers. Figure 4 depicts a conceptual SpaceUM block diagram with 12 V/VS1 switching rails and system-management signal fan-out. The diagram references components that are space-capable and therefore provides a pathway to space-borne VPX applications.
[Figure 4 | Pictured is a SpaceVPX SpaceUM +12 V/VS1 (20 A/240 W) power and system-management distribution conceptual block diagram.]
There are several notable items to recognize in the SpaceUM diagram. First, the A_VS1 and B_VS1 PSU inputs are put together in a premuxed configuration. Premuxing the power supplies provides improved size, weight, and cost advantage versus repeatedly power-muxing and power-switching VS1 for each payload slot.
The blue-colored boxes describe the salient attributes associated at the power-muxing stage in the architecture. The attribute summary within the blue boxes includes an area estimate, current rating, effective channel impedance, and other significant features and functions provided by the smart power-switch controller (SPSC) device. (Figure 5.) The SPSC is a current-class agnostic eFuse controller with integrated fault detection, isolation and recovery (FDIR) capability. The device supports inrush current limiting and ideal diode control FET (with one-way current), which is essential for multiplexing between primary and redundant power supplies. Additionally, through the SPSC’s power management bus (PMBus) interface, the local host controller can perform system-management functions including configuration, control, and gathering of housekeeping data over a simple two-wire I2C serial bus – indicated by the blue bidirectional bus line in the diagram.
[Figure 5 | Smart power switch controllers (SPSCs) integrate fast short-circuit protection, fault detection and recovery, and integrated voltage-current conversion in a single reusable device.]
While the SPSC is a common entity in Figure 4’s blue and green boxes, the number and size of the PowerFETs are different based on where they reside in the architecture and the current rating required. As mentioned earlier, the power-supply premuxing enables significant size and area reduction at the payload-switching stage.
The final block in the Figure 4 diagram worth noting is the purple block representing the SpaceUM system-management hub, which buffers and fans out the signals from the SpaceVPX system controller to all payload slots in point-to-point fashion and controls which PSU supplies power to each payload. System-management signals flowing through the SpaceUM include IPMI communication bus, clocks, resets, and general-purpose signals.
Because the full complement of signals must be singularly fanned out to each payload, the number of I/Os required can quickly outgrow the available resources of a typical small microcontroller. In such cases, an FPGA [field-programmable gate array] or multiple discreet buffering/muxing circuits are used. In the conceptual diagram shown in Figure 3, an Arm M0+ microcontroller or radiation-tolerant FPGA are suggested because of their low power, flexible nature, and small size.
The final item to note is the PMBus interface between the SpaceUM host controller and each SPSC. Unlike commercial devices employing PMBus, the SPSCs provide a redundant, nonblocking I2C interface providing redundant PMBus communication between two host controllers, thereby facilitating fault-tolerant objectives that are built into the SpaceVPX standard. Further, since I2C is a multidrop serial bus, the entire interface between the host controller and all power switches is easily implemented with just two pins.
Next stop, VITA 78.0 …
The space community is abuzz with interest for the VITA 78.0 SpaceVPX standard. The idea of a compact instrument for high-performance space computing and sensor networking with exceptional fault tolerance and scalable modularity is compelling. Implementing the standard is becoming much easier as new, purpose-built space-grade components become available that are capable of meeting all the requirements of a full-featured SpaceVPX platform.
To further lighten the design load, industry groups like SOSA have made great strides toward narrowing the scope and configuration permutations derived from VITA 78.0, thereby providing a roadmap for successfully implementing a SpaceVPX-compliant platform in the near term. With the increased adoption of SpaceVPX, industry solutions providers are developing technology that directly services the needs of SpaceVPX platforms by reducing their footprint, increasing their efficiency, expanding their capabilities, and purpose-building them for space missions.
Tim Meade serves as a systems design engineer for the CAES Space Systems Division where he is architecting space-qualified NAND flash, multi-gigabit-per-second interconnect, power management, and eFuse controller solutions. He has been with the company for more than 20 years. Tim earned a BS in electrical engineering at the University of Colorado at Colorado Springs and an MBA in technology management. Readers may email the author at [email protected] with any questions, including a request for native graphics and supporting application/design details identified in this article.
CAES https://caes.com/