GUEST BLOG: Industry 5.0 -- The digital transformation of A&D manufacturing confronts the next phase
BlogMarch 12, 2024
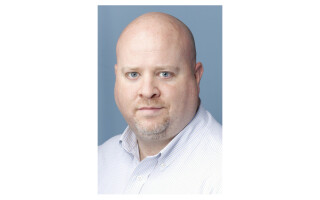
Aerospace and defense (A&D) manufacturers caught up with implementing Industry 4.0 technologies and processes, but now they are facing a new evolution coming in the form of Industry 5.0. The newest iteration could have a number of implications for A&D manufacturers – from cobots and build-to-order to assistive wearables and hyperglobization pullback. The upshot? The humans are back in charge.
Industry 4.0 – the shift that began in the mid-2010s, described as the era of connectivity, advanced analytics, automation, and advanced technology – is pretty much ubiquitous, and Industry 5.0 is on the rise. Industry 5.0 goes beyond more than just new technologies, marked more by the embrace of technology in a societal environment. The European Commission Policy Brief1 shows that this is the overriding belief for Industry 5.0, stating that it “aims beyond efficiency and productivity as the sole goals and reinforces the role and the contribution of industry to society.” Industry 5.0 should work in tandem with the Industry 4.0 approach, which will only be successful if research and innovation are put at the service end of the movement to a manufacturing industry that is sustainable, human-centric, and resilient.
There is also a clear path for North American organizations to incorporate Industry 5.0, with structural changes driven by leveraging digital advances with the right talent and by growing through innovation and human capital.
Industry 5.0 is becoming more established within aerospace & defense (A&D) manufacturing, powered by several key themes:
1. Industry 5.0 builds on Industry 4.0 with a human-centric approach to technology
The groundwork is still being laid for Industry 5.0, but technology is helping move it in the right direction with Internet of Things, additive manufacturing, digital twins, and augmented reality. Manufacturers have become more efficient, quicker, and data-driven when working on projects, giving them the confidence to continue to adopt 5.0 processes.
From design and prototype to manufacturing and in-service support, a “digital thread” has been built by the technology around every piece of equipment. While the focus of Industry 4.0 was on connectivity, digitalization, and automation, Industry 5.0 highlights the importance of human-robot collaboration and the relationship between man and machine, or as The International Centre for Industrial Transformation called them in its late-2022 Industry 5.0 prediction2, “cobots”: “… an add-on to Industry 4.0, building upon the groundwork laid by these smart technologies or cobots.”
Improving the man-machine relationship with 5.0 technologies
New technology applications are emerging as part of Industry 5.0 that focus more on the people executing the manufacturing, particularly to improve their physical capability and safety. In an A&D context, we will start to see and indeed are already seeing technology and equipment from a military background becoming commercialized.
Take the example of the Lockheed Martin Onyx Exoskeleton, which uses artificial intelligence (AI); gathers movement data from users’ feet, knee, and hip sensors; and forwards it to a control module stationed on the waist which instructs the exoskeleton to move accordingly to counteract overstress on the back during operations.
Another example is Boeing, which has been trialing an EksoVest from Ekso Bionics, an upper-body lifting exoskeleton designed to increase productivity and reduce fatigue. Boeing found that it caused an increase in worker speed in test groups of South Carolina mechanics.
Human-centric robotics developments do include the rise of “cobots,” where humans efficiently and safely work next to robots to perform key manufacturing tasks. As part of its “Smart Factory 2025” initiative, Audi stated as one of its key aims enhancing this type of human-robot interaction (HRI). Beyond physical technologies, there are also interesting neurological tech applications such as brain-computer interface (BCI), for example at Neuralink (an Elon Musk-owned company in California), giving humans the ability to directly control machines without the physical constraints of the body. It will be some time before such neurological technology is fully commercialized.
2. 5.0 makes manufacturing more appealing to help combat the industry skill shortage
The latest stats from EY3, gathered with the Aerospace Industries Association (AIA) and the American Institute of Aeronautics and Astronautics (AIAA), on the state of the A&D manufacturing workforce show the sector is experiencing the same sort of workforce and skills gaps as the wider manufacturing sector.
As many as 69% of A&D manufacturing respondents strongly agree or agree that their organization’s turnover has significantly increased within the last 12 months, typifying the intense competition and lack of readily available labor. Across current workforces there is a strong skew towards older employees: In terms of workforce age composition, survey results showed that employees aged 55 and older represent over a quarter of the workforce (28%), the highest of any age demographic.
Increase productivity and employee empowerment with assistive wearables
The increasing development and use of the man/machine and technology/human interface can help provide some immediate relief for current older workers and attract new, younger generations into the A&D manufacturing workspace. Assistive wearable tech can help older workers reaching retirement age achieve more power and productivity, putting less strain on them physically and also enhancing safety.
With this increasing digital focus, unlike some traditional views of the sector as a lower-skilled “blue collar” job market, manufacturing is becoming a more exciting and desirable workplace once again. With more cutting-edge manufacturing and engineering tech, high-skill and well-paid jobs are becoming available as manufacturing becomes smarter.
A&D manufacturing-to-order – the effect of hyperpersonalization on manufacturing
It’s not only employees who stand to benefit from a more people-centric approach within Industry 5.0. Hyperpersonalization is becoming an expected part of everyday life for consumers: think of real-time mobile alerts when walking past a shop or advertising board for a brand or product, or even dynamic digital price tags as individual consumers shop for goods.
This move towards personalization and individual buyer requirements is already reflected on the production side by customers looking for A&D assets and equipment. Make-to-order, configure-to-order, engineer-to-order, and assemble-to-order are becoming common requirements for A&D equipment manufacturing. Smarter factories and digitally focused products provide that coherent digital thread that can feed data back into the manufacturing process to enable quick changes to improve design, fabrication, and performance. It’s imperative for A&D manufacturers to be agile and offer a broad range of project capabilities to prevent long delays and loss of business.
A&D manufacturers need to stay agile, which means having some key functionalities in their enterprise software. Take the example of Abu Dhabi-based defense manufacturer Calidus and the manufacturing process for its Light Attack aircraft. Using enterprise software has enabled it to get away from manual processes – spreadsheets and individual data islands – and the company now manages the complex process of delivering an aircraft or change order to a customer, with critical emphasis on getting the right part to the right place at the right time. Data access is standardized across the board, meaning all parties are viewing the same information at the same time.
Getting the building blocks in place now will provide the framework and capabilities to offer increasingly personalized experiences that will come with Industry 5.0.
3. A&D manufacturers shift their strategies toward environmental, social, and governance
A key part of the definition of Industry 5.0 is a focus on societal and sustainability goals and Industry 5.0 will touch all three elements of any company’s environmental, social, and governance (ESG) strategy. The recent EY CEO Outlook4 cited 69% percent of advanced manufacturing executives are integrating ESG as a core aspect of all their products and using differentiated technologies to boost customer loyalty.
Implementing Industry 5.0 will have a huge positive impact on staff acquisition and retention (see key issue #2), especially at a time where workforce competition is extremely high. Upgrading to 5.0 will touch on the human-centric approaches not just on the factory floor, but at a strategic level throughout the company.
Regulations & customers put A&D manufacturing in the environmental spotlight
Environmental sustainability is increasingly under the microscope for A&D manufacturers from both a regulatory and customer perspective. KPMG highlights5 sustainability as a key A&D industry focus: “A&D manufacturers may not be able to reach their goals unless they integrate carbon reduction strategies throughout their ecosystems … This is particularly important within their hugely complex supply chains.”
New technologies and manufacturing models will help A&D manufacturing CEOs. But to address their environmental output, A&D manufacturers need visibility. This is where the enterprise systems they use to manage their entire value chain can help them adopt sustainable and circular manufacturing operations, including supporting manufacturing disassembly for component reuse and assigning sustainability measures and embedding them into business processes.
4. Supply-chain resilience increases as hyperglobilization reduces
Industry 5.0 will also contain a key focus on resilience. Onshoring and repatriation of formerly outsourced manufacturing and shipping are huge focus areas for protecting supply chains while also addressing environmental impacts of long-haul air and sea shipping, reflecting a potential pullback in the hyperglobalization seen over the last few decades.
This supply-chain consciousness is evidenced by the European Commission policy paper6: “The need for a new industrial paradigm, beyond Industry 4.0, has become more necessary over the years in relation to increasingly complex and pressing economic and societal challenges.”
Capgemini reflects this view in a recent report, “Building resilience in Aerospace and Defense”7: “Designing flexible supply chains and responsive manufacturing and reducing dependences on less-friendly states is now a matter of growing importance – giving rise to ‘onshoring’ (bringing sourcing and manufacturing back to the country) and ‘friendshoring’ (bringing these back to allied countries) … To deliver more flexible manufacturing, the massive global supply chains on which manufacturing relies must become more adaptive and more resilient.”
A&D supply-chain management receives boost from enterprise technology
Enterprise technology will increase agility and faster time to insight (TTI) from domestic suppliers to help them better forecast demand and improve the detail they provide across the supply chain. This move comes after a recent survey commissioned by IFS, researching senior decision makers of large global enterprises, found that 72% of those answering had increased their usage of domestic suppliers, rather than international suppliers.
It is promising to see that the IFS study showed that supply-chain management is a top-three priority for organizations to solve by investing in technology. This finding follows on from the increased movement to reshoring; improved supply-chain management will only help in this regard.
Industry 5.0 is still gearing up, but it has the potential to change A&D manufacturing forever, combining smart and intelligent technologies and human-centric principles. Since so many A&D companies have already mastered the Industry 4.0 rubric, they're poised to move on – as Industry 5.0 expands the focus on human-centricity, sustainability, and resilience to make A&D manufacturers more productive, efficient, and profitable.
References
1 European Commission Policy Brief. https://research-and-innovation.ec.europa.eu/research-area/industrial-research-and-innovation/industry-50_en#what-is-industry-50
2 The International Centre for Industrial Transformation. https://incit.org/en/thought-leadership/industry-5-0-what-is-it-and-how-does-it-relate-to-industry-4-0/
3 EY Aerospace and Defense workforce study. https://incit.org/en/thought-leadership/industry-5-0-what-is-it-and-how-does-it-relate-to-industry-4-0/
4 EY CEO Outlook/Aerospace & Defense. https://www.ey.com/en_gl/aerospace-defense/how-can-sustainability-take-flight-in-aerospace-and-defense
5 KPMG report on Sustainability in the Aerospace & Defense Industry. https://kpmg.com/be/en/home/insights/2023/07/im-sustainability-in-the-aerospace-defense-industry.html
6 European Commission Policy Brief. https://research-and-innovation.ec.europa.eu/research-area/industrial-research-and-innovation/industry-50_en#what-is-industry-50
7 Capgemini: Building resilience in Aerospace and Defense. https://www.capgemini.com/insights/research-library/building-resilience-in-aerospace-and-defense/
As Global Industry Director, A&D, Matthew Medley ensures IFS solutions meet the demanding needs of defense operators, in-service support organizations, and A&D manufacturers worldwide. He has served as a management consultant, program manager, and project manager in aerospace, defense, and manufacturing organizations including Porsche, Lockheed Martin, and others. A graduate of the U.S. Air Force Academy, Matt served as a major in the U.S. Air Force, compiling over 2,500 flight hours in the C-130 aircraft. He holds the FAA Airline Transport Pilot and Certified Flight Instructor ratings and has earned multiple postgraduate degrees and certifications including an MBA from Kennesaw State University and PMI’s Project Management Professional certification.
IFS | https://www.ifs.com/