What will the avionics of the future look like?
StoryMay 11, 2023
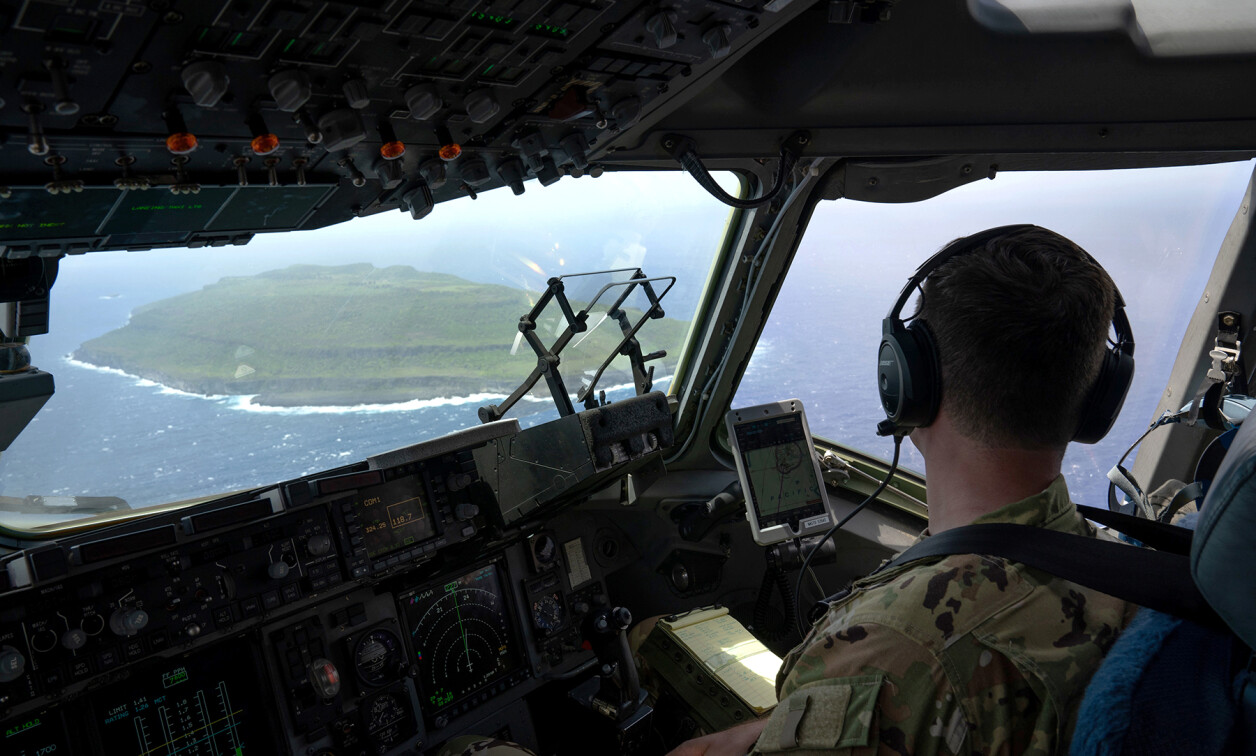
Cockpits featuring multifunction avionics, large touch screen displays, advanced communication systems, high performance/low consumption solutions, and artificial intelligence (AI) capabilities will be part of the future daily life of military pilots.
Military aircraft with analog flight decks are few and far between these days as most have been replaced with modern glass cockpits leveraging advanced embedded hardware and software solutions. Future systems will build even further on that digital backbone to combat complex adversarial threats by enabling a better information flow for faster and more effective responses.
Artificial intelligence (AI) technology plays a critical part in these designs by bringing more complex data processing to enable situational awareness to near-real-time status.
Military applications are “unforgiving,” and “no amount of processing will do you any good if the system can’t withstand the rigors of the environment,” says Emil Kheyfets, director of engineering for Aitech (Chatsworth, California). For that reason “at Aitech, we’ve invested significantly in ruggedizing GPGPU [general-purpose graphics processing units]-based AI systems for the harshest environments to give system engineers the ability to forge new ground in embedded military computing,” he adds. Aitech offers the A179 A178 Thunder, a rugged GPGPU AI supercomputer designed to offer quick processing of critical functions using the NVIDIA AGX Xavier.
Future avionics systems must also enable operations alongside autonomous platforms and manned-unmanned teaming (MUM-T) missions. Future warfare will also require advancements in avionics in terms of size, weight, and power (SWaP), always a balancing act in the realm of unmanned aerial systems (UASs).
Data-hungry video capabilities are impacting avionics requirements both for UASs and piloted aircraft, says Steve Motter, VP of business development at Industrial Electronic Engineers (IEE, Van Nuys, California). “The latency, and the amount of time it takes data to get from the camera sensor to a display or a processing element that can interpret it, becomes really key,” he says.
Open architectures are the future
Future avionics suites are expected to supply more definition, modularity, scalability, and affordability by leveraging open architectures and the reuse of hardware and software components.
Open standards and open architectures also reduce long-term life cycle costs and enable faster deployment of capability to the warfighter. The U.S. Department of Defense (DoD) mandated the use of open architectures in 2019 in a memo calling for the use of a Modular Open Systems Approach (MOSA) in all new programs and upgrades.
For avionics platforms, a MOSA approach that is now required in many platforms is the Future Airborne Capability Environment (FACE) Technical Standard.
“It is very clear that MOSA is the topic of the day when it comes to avionics,” says Mark Littlefield, director, systems products for Elma Electronic (Fremont, California). This is true both in terms of vehicle-control avionics and payload, he adds.
“It really comes down to one key thing: ease of integration,” Littlefield continues. “By using open standards, it makes it so much easier and so much faster, both from a hardware and software standpoint, to integrate your system and not have to build everything from the ground up or port custom designs to new platforms.”
Reusability of avionics software components across multiple platforms is saving time and money.
“This goal of reusability is driving everyone in the industry to adapt designs that previously had been standalone to using common software structures,” says Tad Ihnes, chief technologist for mission systems at Mercury Systems (Andover, Massachusetts). “Ultimately, this will improve customer flexibility and enhance market opportunities.”
Additional advantages include reducing vendor lock and enhancing competition. Fitting capabilities from diverse suppliers also enables designers and engineers to procure best-in-class avionics.
Military customers suffer when they’re locked into a particular vendor on some proprietary architecture, Motter asserts. “Being able to have that open and interchangeable option in a competitive environment is the better approach.”
Moreover, such open options lead defense companies toward more innovation, which decreases acquisition and overall life cycle costs and shortens the time frame required for procurement and development efforts.
“What we’re finding now is that we’re going from that 18- to 24-month cycle to a first deployment down to less than a year and sometimes down into the six-month range,” Littlefield says.
Modernization and life span
Standardization also helps combat obsolescence by enabling incremental technology insertion at the module level.
“There are key functions that are fundamental to flying the aircraft. Those are the base that you build all these other outer functions on. And being able to do that like an ‘app store’ is one of the key objectives that the government wants to try to implement,” Motter says.
MOSA strategies also enable modernization and long-term support for in-service systems based on closed architectures. For example, IEE’s bezel keys can interface with legacy avionics such as MIL-STD-1553, the military standard published by the DoD that defines the mechanical, electrical, and functional characteristics of an avionics serial data bus, he says.
Interoperability and innovation
Interoperability enables integration at the component level in open architecture designs.
In its communication management unit (CMU), Mercury’s compute capabilities enable pilots to quickly visualize threats and their mission objectives. “We created a common user interface for all radios on all aircraft, so you no longer have separate control heads,” Ihnes says. “You have one with a screen that shows you your radios, and you don’t have to know what each radio requires.”
The CMU is designed to replace multiple communication-control heads in an attempt to reduce integration costs, shorten operator training time, and increase overall pilot efficiency. (Figure 1.)
[Figure 1 | Mercury’s communication management unit (CMU) is designed to replace multiple communication control heads, reduce integration costs, shorten operator training time and increase overall pilot efficiency.]
Market trends
At the component level, MOSA strategies will make use of higher-performance processors that can simultaneously handle diverse applications while using diverse connectors.
“The demand now is emerging for 100 Gigabit Ethernet switching products, and we’re trying to get that to market,” says Ken Grob, director, embedded technologies for Elma Electronic.
Elma supplies a collection of backplanes that cover a range of slot configurations for Sensor Open Systems Architecture (SOSA) Technical Standard aligned platforms and the CompacFrame development platforms which enable system development for plug-in cards aligned to SOSA 1.0. (Figure 2.)
[Figure 2 | Elma’s CompacFrame development platforms enable system development for plug-in cards aligned to SOSA [Sensor Open Systems Architecture].]
Interoperability and data-sharing need to continually be improved to prevent the “significant downtime, recertification, etc.,” that can come with integrating new capabilities. Kheyfets says.
SIDEBAR:
Military touch screen tech
Military users are seeking touch screen technologies and large-area displays, which are large high-resolution screens that populate the entire instrument panel of the aircraft.
“Being able to provide that to the operators in some of the worst-case environments – which would be very cold, very hot, gloved hands, high moisture, all of the things that would make the cellphone not work – is really what's going on in the avionics world,” says Steve Motter, VP of business development at Industrial Electronic Engineers (IEE, Van Nuys, California).
To this end, IEE provides rugged smart displays for military applications that require more functionality than just a display and an ordinary touch screen.
“I think that the program managers at a lot of these platform levels and DoD [Department of Defense] levels understand enough to know that they don't know what they will need five years down the road, but having a platform that can accommodate that [uncertainty] is really key,” Motter claims.
At the display level, keeping up with the demand for bandwidth, computing power, and higher-data-rate video and communication without burdening the system with higher power, higher temperatures and lower reliability will be crucial, he says.
At the connector level, the next barrier is accessing appropriate connectors to enable large amounts of information to flow at a high speed in tough or contested environments. Motter terms this situation “difficult,” adding that it is “very challenging to get something that can support six gigabits per second or 10 gigabits per second, as that’s much higher than what we did 10 years ago.”
His company also provides the 10.4 ARINC-818 airborne MFD [multifunction display] as a replacement for legacy cathode ray tube (CRT) obsolescence mitigation or technology insertion on airborne platforms. (Sidebar Figure 1.)
[SIDEBAR FIGURE 1 | IEE’s 10.4 ARINC-818 airborne multifunction display (MFD) is used as a replacement for legacy cathode ray tube (CRT) obsolescence mitigation or technology insertion on airborne platforms.]