Leveraging GaN for radar and soon GaN-on-diamond
StoryDecember 13, 2016
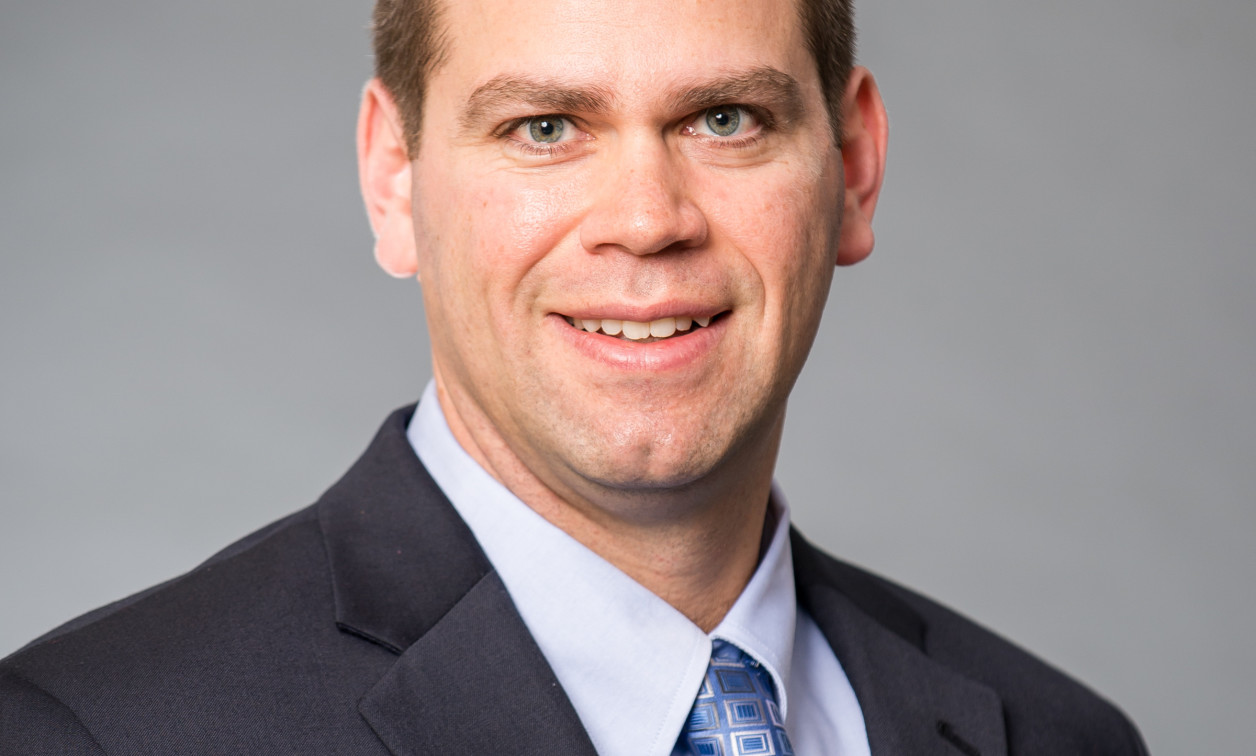
U.S. Air Force Research Laboratory officials in conjunction with the Office of the Secretary of Defense selected Raytheon for a follow-on Title III contract to improve its process to produce Gallium Nitride (GaN)-based semiconductors. In a Q&A with Chris MacDonald, an Engineering Fellow in Raytheon?s Integrated Defense Systems (IDS) Microelectronics and Engineering Technology (MET) Department, he discusses the thermal challenges engineers face with implementing GaN technology into radar and electronic warfare (EW) systems, as well as how GaN-on-diamond could effectively help in the future.
MIL-EMBEDDED: Please provide a brief description of your responsibility with Raytheon and your role within the company.
I serve as the technical lead for the current Title III program. I also serve as the technical lead for many of the GaN process developments as well as the transition and production activities that we have, some of which are internally funded and others that are externally funded, such as the GaN Title III program.
I’ve been with Raytheon for 15 years all with the foundry itself. Earlier in my career I focused on Gallium Arsenide (GaAs) and more recently with GaN. I began working on GaN nine years ago, which was when we started transitioning GaN process into production.
Figure 1: GaN wafer in Raytheon Foundry. Photo courtesy of Raytheon.
(Click graphic to zoom)
MIL-EMBEDDED: U.S. Air Force officials recently granted Raytheon a contract to advance Gallium Nitride-based (GaN) technology, and in the release you state that industry has only scratched the surface with the technology, so what is its impact today and what capabilities will it enable five, 10 years down the road?
This is a similar follow-on program, similar in that it’s Title III and with the Air Force Research Lab. The focus has shifted a little bit from the earlier contract, which focused on the process maturity and manufacturing readiness level. This most recent contract focuses on improving and un-tapping additional RF [radio-frequency] performance. One of the goals is to gain higher performance from our GaN process, while also maintaining reliability and the cost standard that we achieved in the first Title III contract.
In the long-term, five to 10 years down the road, we are looking at alternative material systems like GaN-on-diamond, which we are currently developing. One of the advantages going to diamond long term its thermal benefits. Diamond is the best thermal conductor out there.
MIL-EMBEDDED: In a previous GaN Title III contract completed in 2013, what was the focus on the program and eventual outcome?
In the earlier Title III contract, we focused on transitioning the process into production and on maturing the GaN process in terms of the producibility, cost, and reliability of the technology. Some of the improvements that we saw in that contract were in terms of both cost reduction and reliability. Ultimately that program enabled us to achieve Manufacturing Readiness Level [MRL] 8.
MIL-EMBEDDED: What are some of the challenges engineers face with implementing GaN technology into radar systems?
One of the things that we see with GaN technology is that we were able to achieve higher power. However, with that higher power thermal challenges emerge because we are producing more power and more power tends to produce more heat. Those challenges are one of the reasons we’re focused on GaN Title III, so we can continue to develop and improve the performance. If we can operate GaN more efficiently, it should ease the thermal concerns.
MIL-EMBEDDED: When is GaN not the ideal choice?
In addition to GaN, we also use GaAs technology for many systems we design. We actually will have a hybrid mixture of both GaN and GaAs integrated circuits within our system with the choice being dependent upon the mission and the application, as well as the requirements and functions of those circuits. In many cases we will use GaN for higher power functions in an application where GaAs may still serve a purpose for lower power functions such as phase, attenuation, etc. In other systems we may use a mixture of GaAs and GaN.
When is it not an ideal choice? It depends on the systems, the function, and what we’re trying to get out of that individual circuit.
MIL-EMBEDDED: This technology is expected to be fielded into Raytheon’s Space and Airborne Systems’ Next Generation Jammer (NGJ) program, what are some the benefits associated with using this technology in the program?
Some of the benefits we are going to see will be in terms of both performance and cost. Those benefits will then translate at the system level to size and weight reduction, while improving some of the performance of the actual radar itself. These enhancements will spread to the NGJ program as well as to our radar-based systems such as the U.S. Navy’s Air and Missile Defense Radar (AMDR) and Enterprise Air Surveillance Radar (EASR).. The improvements can be used across any of our GaN-related systems or applications.
MIL-EMBEDDED: What other military applications are likely to take advantage of GaN technology? Electronic warfare? Communications?
GaN is at the heart of many Raytheon systems such as ground and sea-based radars, electronic warfare systems, missile applications, communications, etc.
Applications that will incorporate GaN components include EASR for aircraft carrier and amphibious class ships, as well as AMDR for DDG-51 Flight III destroyers.
MIL-EMBEDDED: How will it impact those applications?
GaN’s impact with these platforms is similar to its affect on the NGJ program, it enables performance and cost benefits. When you move from GaAs to GaN technology, you can get five to 10 times the power, thanks to the increased power density, which in turn improves performance and efficiency.
Christopher J. MacDonald is an Engineering Fellow in Raytheon’s Integrated Defense Systems (IDS) Microelectronics and Engineering Technology (MET) Department. He joined Raytheon in March 2001 and was promoted to his current position in 2016. MacDonald is the lead process engineer and the section manager for the Wafer Fabrication Engineering in the MET Department, which provides development and processing engineering support for Raytheon’s key Gallium-Nitride (GaN) and Gallium-Arsenide (GaAs) compound semiconductor processes used in the design of Monolithic Microwave Integrated Circuits (MMICs). He received a bachelor’s degree in materials science and engineering from Massachusetts Institute of Technology and a master’s degree in manufacturing engineering with a concentration in materials processing from Boston University.