Scalable assurance: A new approach to sourcing rad-hard electronics for space
StoryJune 09, 2023
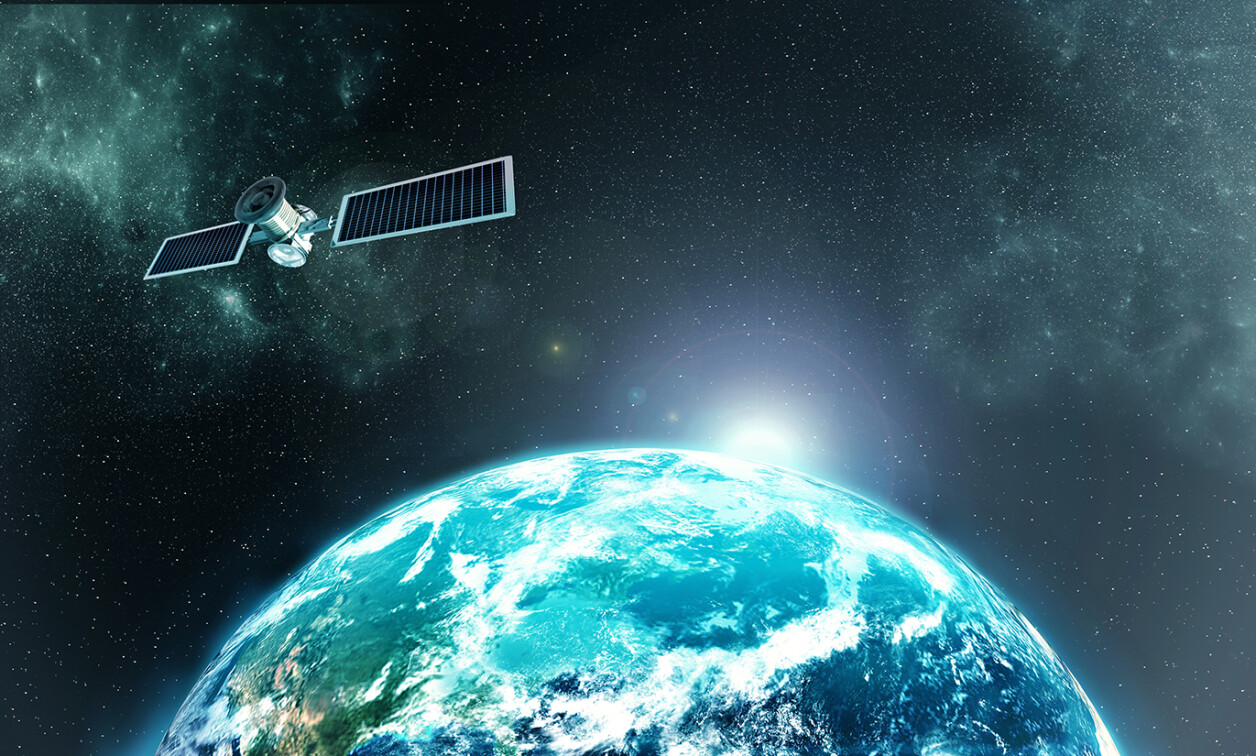
The concept of “scalable assurance” is now at the forefront of the military space electronics industry, reshaping the way rad-hard designs are developed, acquired, and employed.
In the arena of rad-hard electronics destined for use in space, there has been in the past few years a brighter spotlight on the rise of commercial off-the-shelf (COTS) components and open standards. While these developments continue to hold sway, the industry is witnessing an expanded array of demands from military customers.
The call comes now not just for components that can withstand harsh radiation environments, but for a broader spectrum of reliable solutions that can be scaled to fit the mission at hand. As the market diversifies, so does the need for a range of reliability, packaging, test levels, and radiation-performance options.
A new frontier in rad-hard electronics
Scalable assurance, in the context of military and aerospace applications, refers to the ability of a system or a component to offer varying levels of reliability and performance based on the mission requirements. This concept involves the use of a tiered system of products that range from simple COTS devices all the way up to parts that meet stringent military standards. This scalability is also reflected in the radiation tolerance of the devices, levels of which can vary from radiation-tolerant to radiation-hardened.
The scalability of these systems enables mission designers the flexibility to use components that are so-called fit for purpose, rather than having to overspecify components to meet the most demanding environments. This approach not only enables cost savings, but it also ensures that the devices perform optimally in the intended environment.
As military customers increasingly demand versatile solutions, the industry has responded with an approach that offers flexibility without compromising on quality or performance. Bob Vampola, vice president of the Microchip Technology (Chandler, Arizona) aerospace and defense business unit, says integrators are placing an increasing emphasis on tiered levels of radiation performance.
“Military customers are looking for levels of reliability from COTS devices, all the way to QML-V and QML-Y, as well as supporting radiation performance from radiation-tolerant (RT) all the way up to radiation-hardened by design (RHBD),” Vampola says. [Editor’s note: The traditional QML-V certification for radiation-hardened parts means that they are compatible only with legacy assembly processes and does not account for new-generation assembly techniques; QML-Y enables space systems manufacturers to use the latest technologies – including things like flip-chip on ceramic – while ensuring verification for each device produced.]
Turning to commercial parts
Meeting these demands while maintaining reliability isn’t easy, but the commercial chip industry and COTS components have helped. Manufacturers are offering a range of products and seeking new sources to help supply them.
The future of rad-hard electronics depends on companies like his finding cost-effective solutions to meet the evolving requirements in the world of rad-hard and rad-tolerant tech, says Anton Quiroz, CEO of Apogee Semiconductor (Plano, Texas). Apogee has dipped into the commercial space for help in that area, Quiroz notes. (Figure 1.)
[Figure 1 | Apogee Semiconductor’s RadFlex is a semicustom logic process intended to take designers from concept to device in months at 30 Krad and 300 Krad.]
“We use commercial foundries ... that not only maintain the costs low, but we get very high yield,” he continues. “Our yield for our products is very high … usually greater than 90%.”
The need for commercial foundries is driven by the challenge of creating electronics that are both rad-hard and can withstand higher voltages, which are “two things that don’t go very well together,” Quiroz notes. “So we’ve seen a push toward the area of investing more in commercial, like on feature sizes and on processes that can withstand higher voltages and be rad-hard.”
Volume also plays a critical role, Quiroz points out. “For that, you do need to run quite a bit of volume because you need to look at tens of thousands of data for tens of thousands of devices. It’s so difficult to do something like that when you’re just building ten of something,” he says.
The global semiconductor supply-chain challenge
Adding to the complexity brought by military space requirements is the ongoing global semiconductor supply-chain challenge. This has had ripple effects in various sectors, including military space applications. Fortunately, space applications have been less disrupted due to the inherent nature of the industry, Vampola says.
“Because military space applications require components which typically have longer lead times, customers are accustomed to ordering devices with plenty of buffers,” he explains, adding that the key lies in the precise management of inventory to cater to industry needs amid supply chain hurdles.
Even so, supply chain issues continue to plague the industry. Given the intricate nature of these electronics, waiting for chips means projects can be stalled for extended periods. This delay can result in cost overruns, delayed deployments, and potential loss of competitive edge, making this issue a crucial concern for industry stakeholders.
As a result, some in the industry are taking matters into their own hands by creating new ways to streamline their operations. Joel Placito, chief engineer at Aethercomm (Carlsbad, California), says his company has figured out ways to adapt to the shortage and develop radiation-resistant technology despite the long lead time for chips. (Figure 2.)
[Figure 2 | Aethercomm’s space products group parts are intended to deliver radiation-hardened, space-qualified hardware at TRL-9 (the highest level of technical readiness) across low-Earth orbit (LEO), geosynchronous Earth orbit (GEO), and lunar missions to support global cross-domain warfighter connectivity.]
“I would not say I’ve seen the shortening [of the supply chain] just yet,” Placito says. “When the supply-chain challenge [initially] hit us, it forced us to revamp the way we do business in engineering, in particular. We sat down and had to flowchart our entire process and find ways to involve the purchasing and planning department early in the process because it was going to destroy all our schedules.”
The company focused on the availability of components, which is “just as important as performance and anything else,” he adds. The company now designs and develops around parts that they know already exist and they have access to, and they even have a space-parts library to ensure easy access to those parts in response to the uncertain supply chain. This approach is yet another arm of the scalable assurance method.
The role of AI
Although the demand for rad-hard solutions to enable artificial intelligence (AI) in space systems – AI being “the” hot topic in nearly all other electronic and other realms – is not quite at fever pitch yet, the industry is in fact bracing for it.
Placito suggests that while they aren’t seeing much yet in the way of requirements on the AI front, “as those requests come in, we will be able to utilize and transfer again some of that background and technology over into – hopefully – some of these coming space applications.”
On the other hand, Microchip’s Vampola notes the critical need for onboard processing of data, and thinks that AI may be able to help in this area. Microchip is positioning itself to provide solutions to enable AI in all types of space systems, he says.
It is important for warfighters to have “the ability to download intelligence rather than raw data, as the download links do not have enough bandwidth to handle the larger data processing that occurs with newer high-resolution sensors,” Vampola explains.
A wide-open future for rad-hard electronics
From the resurgence of space exploration to the development of constellations, there are a host of new opportunities in the rad-hard electronics industry, and companies are aligning themselves accordingly.
“The push for a lot of the constellation work really just aligns wonderfully with our product mix and our business model,” Placito says.
For Vampola, “everything is in play,” with space exploration extending to “space sciences, manned flight, interplanetary travel, cislunar, proliferated LEO, and lunar LEO.” (Figure 3.)
[Figure 3 | Microchip’s VSC8574RT PHY is designed to support both copper and fiber interfaces for added flexibility in space applications.]
With a focus on scalable assurance – in whatever form that might be – the industry is gearing up to provide solutions that cater to diverse needs while maintaining reliability. While reliability in space is a challenging path fraught with technical and logistical hurdles, Placito believes that he and his peers are ready: “We’re excited to see how that’s going to develop and how we hopefully can continue to support that.”