ARL scientists use 3-D printing to fabricate ultra-strong metal parts from powder
NewsMarch 05, 2019
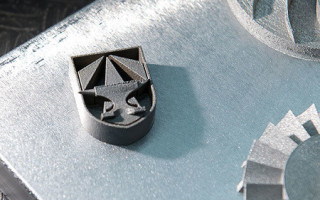
ABERDEEN PROVING GROUND, Md. Researchers at the U.S. Army Combat Capabilities Development Command's Army Research Laboratory (ARL) are confident that soldiers needing replacement parts will be able to turn to 3-D printers in the future to rapidly deliver reliable and ultra-strong metal parts.
ARL scientists recently reported progress in using an alloy -- originally developed by the U.S. Air Force -- in making metal parts. The Army adapted the metal, called AF96, to powder form; using a method called Powder Bed Fusion, the 3-D printer's laser selectively melts the powder in a pattern and coats the build plate with more layers of powder, and the process is repeated until the part is finished.
"I think it's going to really revolutionize logistics," said Dr. Brandon McWilliams, a team lead in the lab's manufacturing science and technology branch. "Additive manufacturing is going to have a huge impact on sustainment." Even as the 3-D metal printing trials continue, McWilliams cautions that realizing the dream of quickly printed, reliable 3-D metal parts is still a long way off. He does, however, believe that its benefits will be substantial: "You can really reduce your logistics footprint," he said. "Instead of worrying about carrying a whole truckload, or convoys loads of spares, as long as you have raw materials and a printer, you can potentially make anything you need."
For Army applications, the key to usage is certification, or whether the 3-D printed parts will work as needed in a battlefield scenario. "We've printed some empeller fans for the M1 Abrams [Main Battle Tank] turbine engine and we can deliver that part -- they can use it, and it works," McWilliams said. "But it's not a qualified part. In terms of a battlefield scenario that may be good enough to be able to get your tank running again for hours or days if that's important to the mission, but on the other hand, we still need to be able to answer, does this perform as good as the OEM [original equipment manufacturer] part? Does this perform better?"
According to the ARL researchers, it comes down to two main points: One is using these parts for battlefield sustainment, the replacement of existing parts and supporting legacy systems; the second piece, they say, is about future systems: "That's where we're more integrated with the OEMs and industry to see the things they're working on and see how we can make things better to really push the state-of-the-art," McWilliams said.
The ARL says that it is is working closely with industry and academic researchers to model new alloy designs, perform computational thermodynamics, and expedite the process to get the materials to soldiers in the field.