Flying vehicles: Are we there yet?
BlogOctober 22, 2020
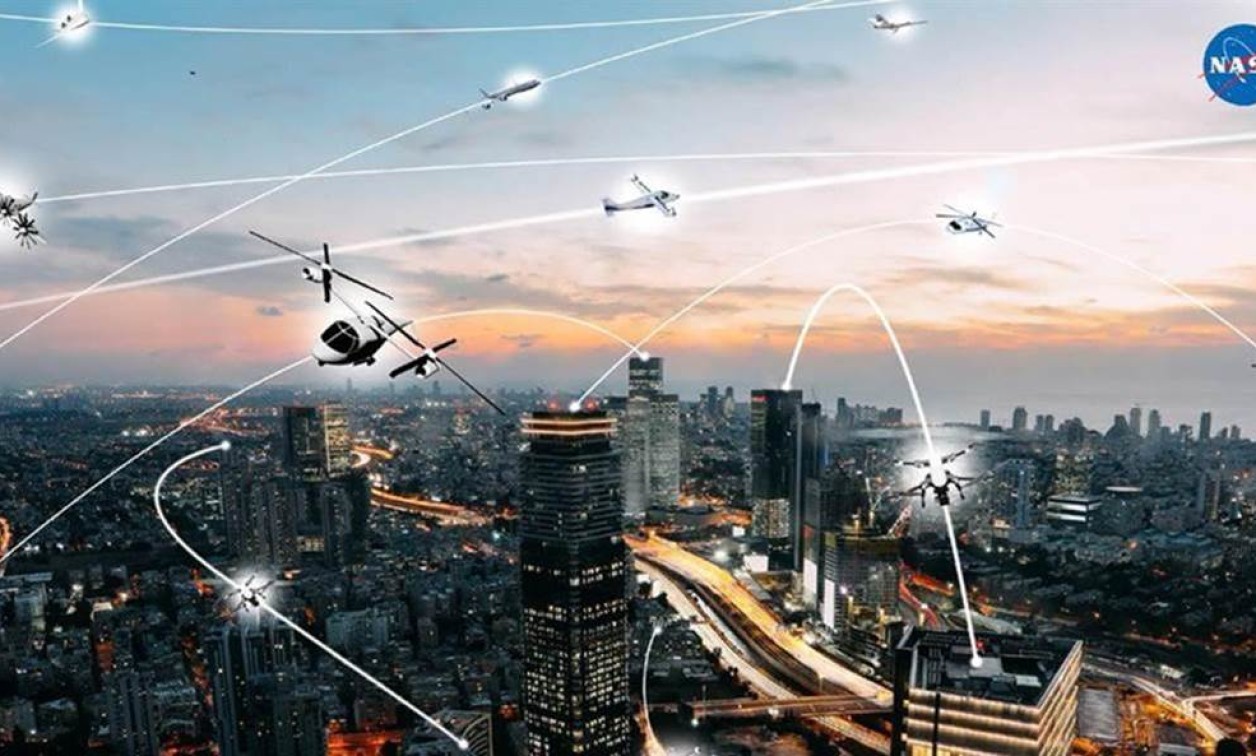
By Will Keegan, Lynx Software Technologies
Flying cars are being demonstrated and are close to becoming a reality as the urban mobility segment experiences significant investment. We’ve also had discussions with an automotive manufacturer who is looking to build avionics platforms. So that got me thinking about the way in which the avionics and automotive industries will come together. It’s already happening.
What gives me so much confidence that flying cars will become reality? Three things:
- The role of artificial intelligence (AI) in the design process
- How the certification world is already adapting to applying safety certification to unmanned systems, including drone deliveries, taxis, conventional aircraft, and helicopters
- Which system architecture will be victorious?
To be clear, while I reference a flying car above, which obviously implies more of a commercial application, the battlefield is changing. There will be a diverse range of craft deployed in the future, including purely autonomous systems and others with pilots. These systems will be connected with aircraft controlling drones and collaborating with troops on the ground and at sea.
When I am driving my two-year-old, Connor, to an activity, I am confident of getting him to the place safely. That said, I know he will feel the journey is taking an inordinate amount of time, will feel I should be moving faster, and may doubt we’ll ever arrive! This is NOT going to be a simple journey to the store, though. This is going to be a trek across several continents.
Ground zero
I was inspired by a visit with a Tier 1 automotive supplier that gave me insight on ground zero of this problem space. The supplier makes models of passengers, their relationships with the vehicle, and all the features of the vehicle and trace that into computer parts. These graphs are insanely complicated -- the number of nodes that connect people to capabilities, the dependencies of the capabilities, and the pressures these capabilities put onto computer parts. Moreover, bear in mind that the models I viewed related to relatively simple features put into regular cars.
These graphs become dramatically more complex in order to fully consider autonomous platforms and the fact that functionality might not be available due to contention for system resources inside multicore processors. The certification teams had some veto power to block the use of certain components when they are not satisfied that those will deliver the required level models of safety. But if these experienced, methodical teams are able to mature their models and go through the rigorous steps of certification, this dream will be realized.
Artificial Intelligence
Simply put, artificial intelligence (AI) is here and will be deployed. The better question is where it will be applied and in what time frame. To me, the “eyes” of these craft have to be computers. There is simply too much data to process in too short a period of time to consider any other type of approach.
At the other end of the spectrum, I cannot see AI playing a part in the mission-critical electronics portion of these designs. A business acquaintance that works in the EDA industry told an interesting anecdote in which an AI platform was used to help in the design stage of a specific semiconductor chip to achieve timing closure.
To those not in the industry, "timing closure" means enabling the part to operate at a target frequency. Traditional manual methods had failed. The AI system enabled the platform to beat the desired target and no one was able to work out how the result had been achieved. This is probably fine for a component in a smartphone or laptop, but in mission-critical systems, authorities and manufacturers must know more about what is inside the magic box as opposed to simply seeing the decisions that are made. I think there are also opportunities for AI algorithms to improve fuel (battery) efficiency based on weather patterns, speed of travel, weight, etc.
Certification
If I start with the bottom line up front, I believe that the path for certification has to change. The existing certification infrastructure is built around old technology and there are three elements straining this system. First, the technology is more complex. Second, the volume of “things” in the sky is increasing. Last, the use cases of these craft are broadening.
Think about a city like London where drones are delivering packages, as people take off in their urban mobility craft. This does sound a little “Jetsons” but I assure you that people are starting to purchase property there with a view to landing craft on their roofs. This eventuality needs a new level of rigor to break down this problem; up to this point, such a level of complexity has not appeared There exist some serious process gaps for new technology. Okay, what am I proposing?
- We have to embrace the use of computers in the validation phase to determine if the work that has been completed is legitimate. At the end of the current processes, there is a mountain of paperwork. Humans then need to provide an assessment on the system as to whether it is safe; we have reached the point where this is simply the wrong path
- Certification should not simply be about following a process; I recently found a paper that asked the provocative question to software vendors: What is the intent of your product offerings? The current certification breaks things down into thousands of low-level tests. The supply chain works their way methodically through these tests to get the stamps and certifications … but without the bigger-picture questions being answered appropriately about whether the offering is truly an operating system or a hypervisor or a container distribution mechanism, how do we know we are really verifying the capability (and limitations) of these software modules appropriately?
I have seen a full spectrum of system architectures and approaches, from some incredibly robust system approaches to certification through to some start-ups who are simply focused on quickly getting something in the air.
System architectures
The system architecture in today’s planes have two distinct computer systems with hardwalls between them. There are, of course exceptions, when the mission system can intervene in the event of a major problem. In a car, there is more intermingling of systems and fluidity of information flows with strong connectivity.
Clearly, this design has to be done appropriately to ensure there is robust immunity to security compromises. When implemented correctly, this approach enables resources to be dynamically allocated to perform local processing near a sensor to improve latency.
The other aspect of this is dealing with failures. In autonomous vehicles, if a function fails, other resources can be allocated to support this function. As an example, if a processor in the ADAS [advanced driver-assistance system] has an issue, the main processor in the infotainment system can be reallocated to support this processing. Although the passengers miss out on listening to the BBC World Service for the remainder of the journey, they at least are able to land safely.
I am aware of several traditional aerospace and defense companies starting to explore these types of architectures. Coupled with some interesting advances that the semiconductor companies are making in next-generation automotive platforms in terms of strengthened security and isolation of processes, my sense is that this is the approach that will win out in the longer term.
Will Keegan is chief technology officer, Lynx Software Technologies. Readers may reach him at wkeegan@lynx.com.
Lynx Software Technologies lynx.com